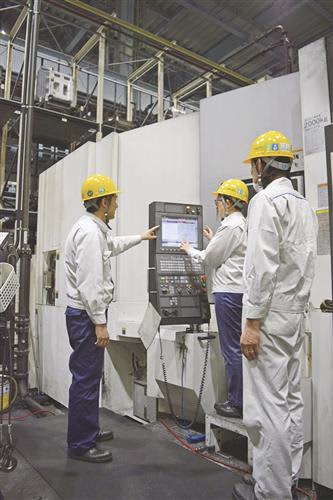
「コウグハソンノ『ヨチョウ』ガアリマス」。AI(人工知能)が、異常が起こりそうなわずかな変化を検知し、機械の切削加工を自動で止めたり、再開したりする。工作機械メーカーのオークマ(本社愛知県大口町)は、切削加工時の「AI加工診断機能」を最新機種に順次適用させ、生産現場のトラブルを未然に防いでいる。
ワークを守る
AIが計算した正常な加工との乖離(かいり)具合を「異常度」として診断し、異常が見られれば加工を中断、工具を退避させる。さらに、新しい工具に自動で交換し、加工を再開する。朝、現場に来てみたらワークが出来上がっていた―。そんな、自動化された生産現場を支える技術だ。
開発したのは4年ほど前。工具の破損で費用がかさんだり、折れた工具がワークに埋まって使いものにならなくなったり、工具が大きい場合には機械そのものの故障につながったりと、困りごとの声が社内外から寄せられていた。
破損が起こる前に診断ができないかと、自社工場で検証を始めた。人が感知できないような例えば振動や音など、ほんのわずかな異常の予兆をAIが的確にとらえる。工作機械の頭脳といわれるCNC(コンピューター数値制御装置)に組み込んでいるため、診断は高速だ。
異常を検知する技術は、切削加工時の負荷を監視する形で過去にもあった。しかし、工具も、加工する素材も多種多様な中で、一つ一つに対して計算処理し、正常と異常との境界線となる値を設定するのは煩雑かつ、難しかった。「切削を知り尽くしたオークマだからこそ、AIとの融合で診断という作りこみができた」と、研究開発部知能化技術開発課の曽我部英介主事(36)は胸を張る。
これまで、工具の折れ方や切り粉の詰まり方など、14万穴以上の加工データを用いた診断の検証を自社で行ってきた。実際、効果が出ている。直径8.2ミリの細長い「ガンドリル」の場合で、工具破損によるワーク不良が3~4カ月に1回あった発生回数が、AI加工診断機能の適用後、3年経過してもゼロ。1本あたりの工具の使用時間は約6割延長でき、使い切れるようになった。
「機能をオンにすればあとはAIがワークも工具も守ってくれる」と、大口工場の山口裕貴係長(43)。機能の適用当初は、「AIって、本当に大丈夫なの?」といった懐疑的な雰囲気が現場に漂っていた。しかし今では、「AIと一緒に働いている感覚」と打ち解けた。
10分の1に短縮
「実現できれば、開発期間は10分の1に短縮できる」と語るのは、日本ガイシ(本社名古屋市)の小林茂社長(63)。同社は、材料開発の分野で、AIなどを駆使して新材料を効率的に探索する「MI(マテリアルズ・インフォマティクス)」の実用化を進めている。
これまでの実験データや、報告書などをAIに学習させ、高速実験を繰り返しながら、革新的な材料創出を目指す。MIは樹脂や染料など、有機材料を扱う企業ではすでに導入が進んでいる開発手法。ただ、構造が複雑な無機材料であるセラミックの場合は、実用化が難しいとされてきた。
現在は、100年分の実験記録や、1万件以上の報告書、高速実験のデータなどをAIに学習させ30年までにグループ全製品の材料開発に適用する考えだ。小林社長は「現在も一部の物質については、3分の1まで短縮することに成功している。開発が短くなり、提案が速くなるのは大きなビジネスチャンスだ」と強調する。
◇◇◇
生産性向上への要求が強まる中で、製造業のデジタル化が進化している。中部シンものづくり第2章では、デジタル化の新潮流を、中部各社の事例を通じて紹介する。