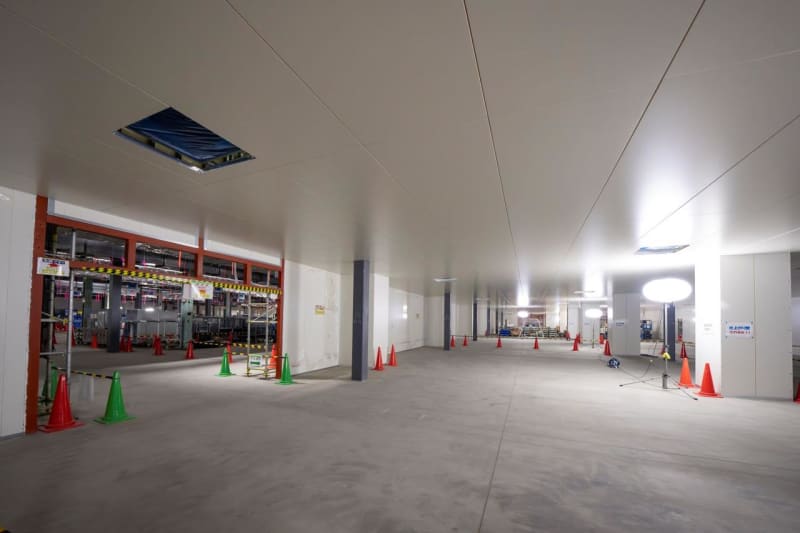
2024年4月16日、日産自動車は横浜工場内に建設中の全固体電池の生産を行うパイロットプラントを、報道陣に公開しました。さまざまな意味でEVの性能と生産ポテンシャルを大きく変える「ゲームチェンジャー」が、いよいよ本格的な普及に向けた第一歩を踏み出すことになります。技術的な革新と同時に日産は、今後のクルマづくりにおける「現場の課題」に対応した働き方改革についても、取り組みを進めているようです。
創業の地に、新たな「はじまり」の拠点が誕生
実質的な走行距離が短い、充電にいちいち時間がかかる、なにより価格が高い・・・「全固体電池」はそんな、電気自動車(BEV)に対するネガティブイメージを一気に覆す可能性を秘めた、テクノロジーです。
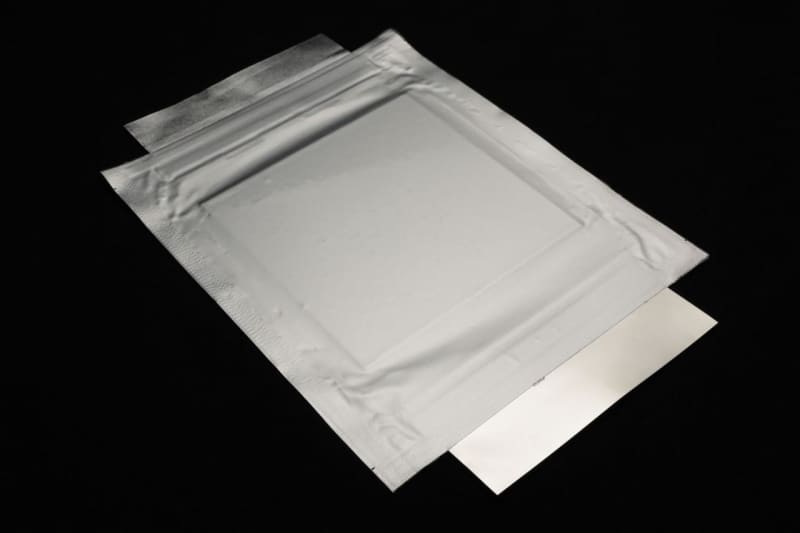
国産メーカーとしていち早くBEV「リーフ」を量産・市販した日産自動車もまた、その実用化に向けて積極的に取り組んできました。だからこそ2022年には他社に先駆けるカタチで試作生産工程の一部を報道陣に公開。その際には、2024年度までに量産化に向けたパイロット生産ラインを横浜工場(神奈川県横浜市)内に設置、2028年度までに市場投入する計画を明らかにしています。
そのスケジュールどおり、2024年度中の稼働を目指して新設中の全固体電池生産ラインを含むパイロットプラントの見学会が今回、開催されました。建設が進められている横浜工場は、日産自動車にとって創業の地にあたります。そんなランドマークから日産は、新たな一歩を踏み出すことになります。
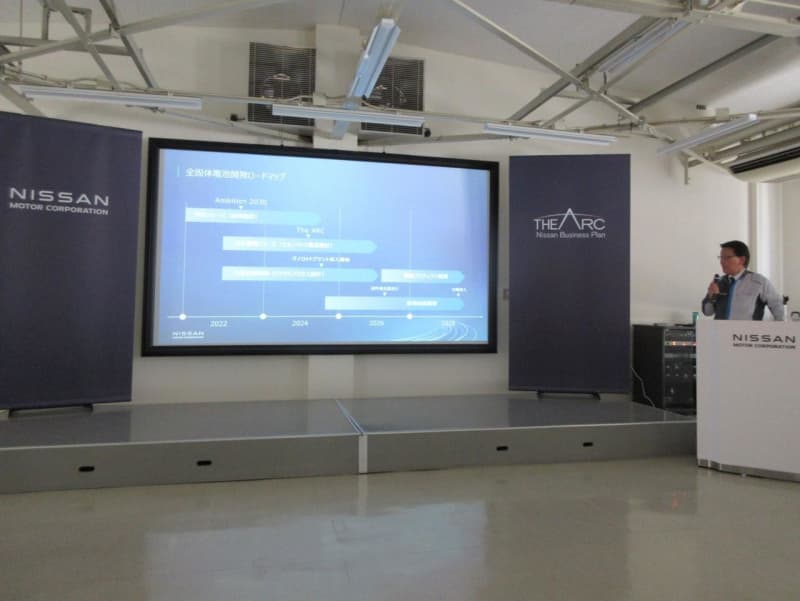
実地見学に先立ってのレクチャーでは、2年にわたる研究開発の経過がハイライトの形で紹介されました。活用する素材の検証、生産工程上の課題解決、熱暴走を含めた安全性への対策などの研究が着実に進められてきたといいます。
今回のパイロットプラントにおいて、研究室内でのラボスペックから市販車への採用を前提とする車載スペックへのステップアップに向けて、さらに一歩進んだ取り組みが始まります。
製品化に必要なあらゆる「プロセス」の最適化を模索
パイロットプラント内部は大きく分けて、「電極工程」「セル工程」「モジュールパック工程」「化成工程」という4つのエリアで構成されています。現状は建屋の環境整備が進められている段階でまだガランとした印象ではありましたが、設備の搬入は2024年8月からを予定しているそうです
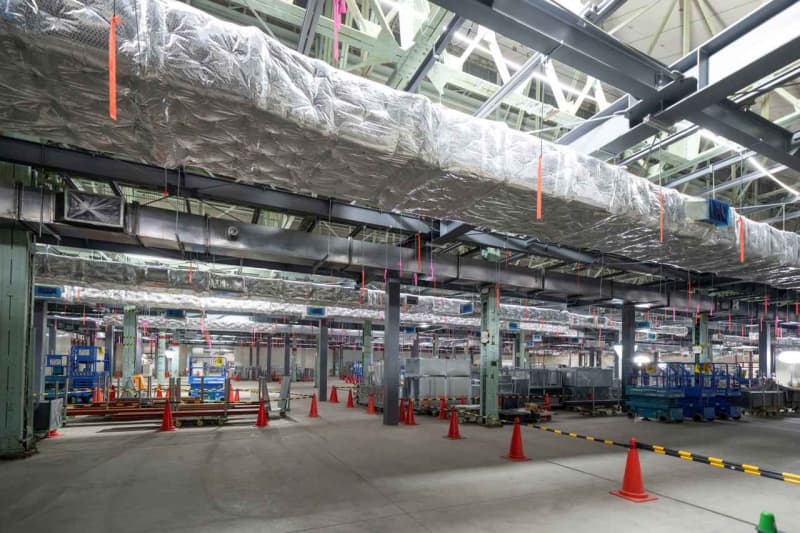
このプラントでは製品/生産技術の開発フェーズを経て2026年度から生産能力(生産性)向上のフェーズに入り、2028年の生産フェーズへの移行を目指しています。素材系技術の検証・進化と生産工程の設計・熟成を並行して進めることになるようです。
日産の生産技術開発については改めて詳細に解説したいと思いますが、全固体電池の生産プロセスは、電極の原材料となる物質を均一に混ぜる作業(分散)や、フィルム化されたものを均等に加圧して厚みを均一化する作業などに、高度な精密さが求めれるそうです。
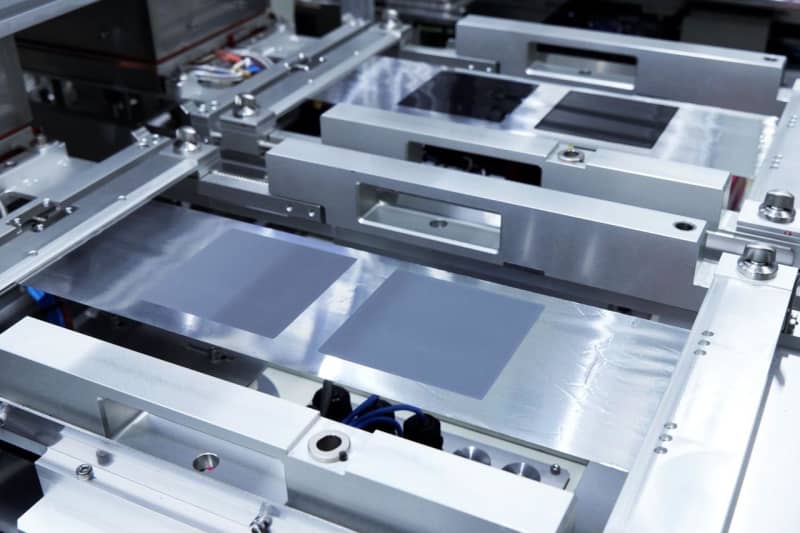
新設されるパイロットプラントでは、そうした各プロセスでの生産技術開発における課題解決を目指した検証、進化が進められます。料理で言えば、目的とする味を表現するための最適な食材の最適な組み合わせを確かめながら、最適のレシピを確立していく作業が並行して進められるわけです。
興味深いのは、エンジンや従来の生産現場で培われたさまざまなノウハウが、全固体電池製造工程の進化にも生かされている、ということです。たとえば電極工程における品質悪化について問題、仮説、実験、検証のスキームにも、かねてから熟成された技術が生かされているそうです。
将来的に、このパイロットプラントで熟成された工程、生産技術は世界各地の生産拠点に展開されることになります。そのノウハウは日産本体だけでなく、サプライヤーに対してもおそらくは提供されることになるのでしょう。いわば、次世代パワートレインの生産作業に従事する作業者たちのための、トレーニングセンター的な役割も担うことになります。
全固体電池が搭載される最初の「新型BEV」は、そうとうレア?
今回の見学会では、パイロットプラントの紹介とともに、車両の製造工程における新たな取り組みも紹介されました。「スマート工程」と呼ばれるもので、組み立てラインをメインラインとサブラインに分けることで、作業における負荷の調整を図ります。
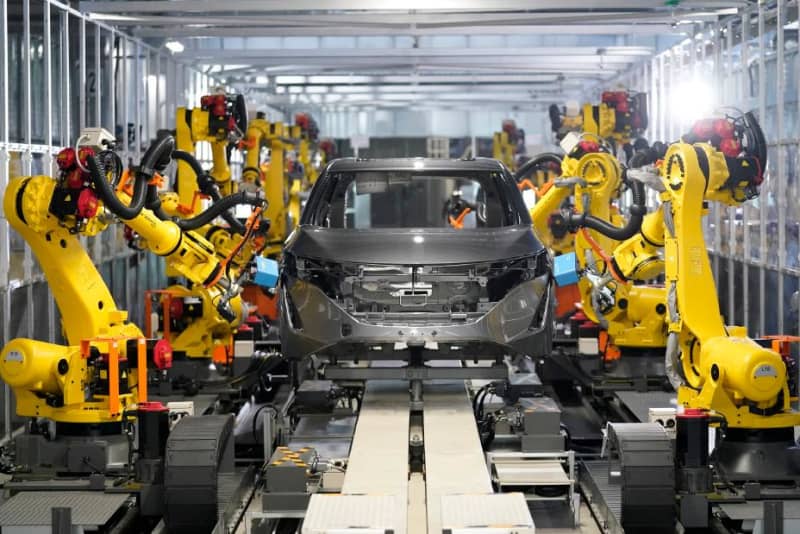
日産では栃木工場を皮切りに、生産現場で2030年までのカーボンニュートラル化を目指した「ニッサン インテリジェント ファクトリー」化がすでに進められています。今回のスマート工程は、ライフステージバランスの最適化という、より人材活用の「スマート化」に寄り添った「働き方改革」につながる活動と考えていいでしょう。
とくに時間の制約が強い育児世代や身体能力の低下を伴うシニア世代が効率的に働く環境としては、非常に優れている、とのこと。すでに福岡県苅田町の九州工場でも導入、検証されたもので、今後予想される労働人口の減少といった、社会的問題に対応することが可能になりそうです。
ちなみに日産は、2021年11月に発表された長期ビジョン「Nissan Ambition 2030」において、2030年度までに電気自動車19車種を含む27車種の「ワクワクする」新型電動車を投入することを明らかしています。さらに2024年4月に発表した中長期経営計画「The Arc」では、次世代EVのコストを30%削減し、2030年度までにICE車と同等のコストを実現することをコミットしています。
そうした新たな躍進を支えるために、全固体電池だけでなくすべてのモデルを含めた開発・生産環境の整備にもまた、革新が求められていることは確かです。
それにしてもどんな新型EVから、市販スペックの全固体電池が搭載されるのでしょうか。たとえば欧州では「キャシュカイ」や「ジューク」のBEV化が決定。日産、インフィニティブランドを合わせて、電動車のモデルミックスは55%以上と目標設定されています。
パイロットプラントの生産としては、かなり限定的な台数からのスタートとなることは間違いなさそう。「ハイパフォーマンス」で「レア」な日産車と言えば、真っ先に思い浮かぶのはたとえば「GT-RのEV版!?」ですが・・・果たしていかに。