パナソニックは5月28日、滋賀県にある冷蔵庫のグローバルマザー工場である草津工場を報道陣に公開した。多品種少量生産に対応する最新の「ミックス生産方式」や、2030年度に金額ベースで150%の伸長を目指す事業戦略も明らかにした。
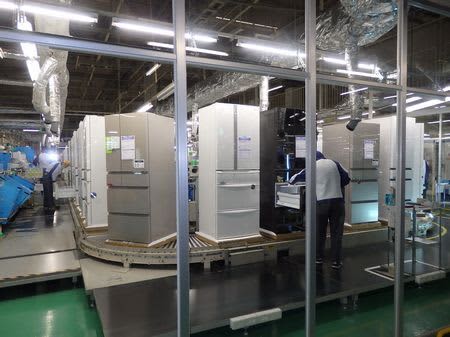
国内で「ダントツナンバーワン」、海外事業も注力
パナソニックが草津工場を報道陣向けに公開するのは10年ぶり。くらしアプライアンス社常務でキッチン空間事業部の太田晃雄事業部長が語った事業戦略では、2030年度に金額ベースで23年度比約150%のアップを目指す。
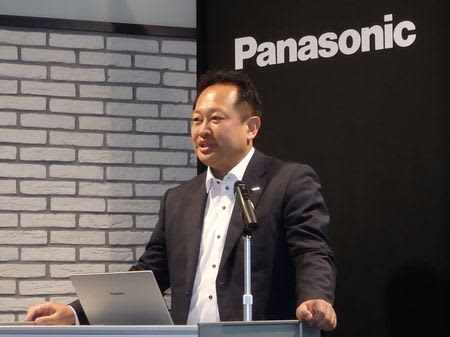
具体的には、現状の国内冷蔵庫市場におけるトップシェアを、「ダントツナンバーワン」としてさらに強固なものとする。同時に、伸びている海外事業に引き続き注力する。
海外では欧州で展開するビルトインや、インド、ブラジル市場などを攻める。現在の国内3分の1、海外3分の2という事業構造は変えず、国内外ともに伸ばしていく形だ。
また4月に発表したリファービッシュ品事業「Panasonic Factory Refresh」で、新たに加わえた冷蔵庫の売り上げを増やしたりして目標達成を実現する。
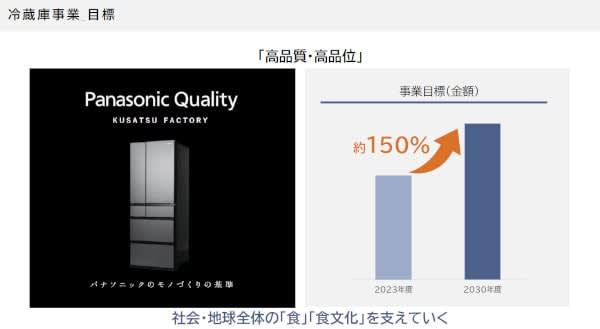
本体幅とウレタンは薄く、でも庫内容量は増える「秘密」
草津工場の操業は1969年。敷地面積は東京ドーム約2個分の約10万平方メートルある。従業員数は約700人で、国内向け、海外輸出を含む冷凍冷蔵庫を製造する。生産能力は一日当たり2000台だ。
さっそく、公開された生産工程を見ていこう。本体サイズが大きい冷蔵庫は、ひとつひとつの部品も大きいのが特徴だ。
主なユニットは前面から「ドアブロック」、庫内ガラストレイや庫内ケースの「庫内ブロック」、エバポレーター(蒸発器)や冷蔵室ダクトがある「冷却風路」、真空断熱材(VIP)やウレタン発泡を注入する「キャビネットブロック」、コンプレッサ(圧縮機)や凝縮器がある「機械室」の五つから構成される。
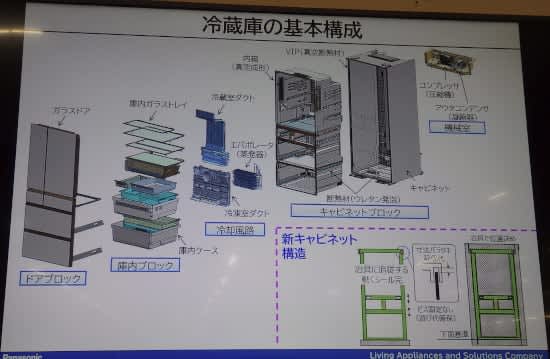
庫内の内箱は、厚さ2.2mmのABSシートという板を、プレスして成型。ウレタン充填設備でウレタンを注入したり、真空断熱材を取り付けたりして断熱性能を高める。食材を冷やす冷蔵庫の基本性能に直結する重要な工程だ。
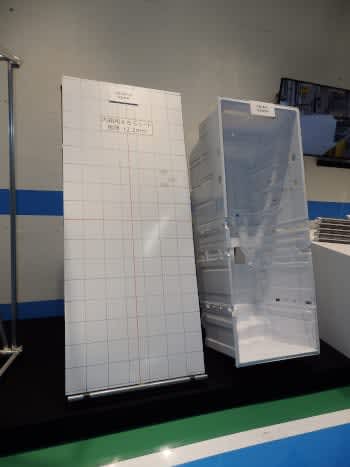
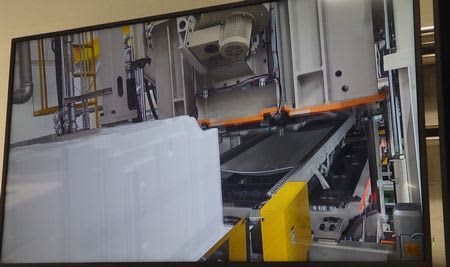
工場ではウレタンをつくるデモを実施。ポリオールとイソシアネートを混ぜて化学反応させると、みるみると膨れ上がりウレタンとなる。膨らみが落ち着いてから触ると、固くなり、少し熱を帯びているのがわかる。
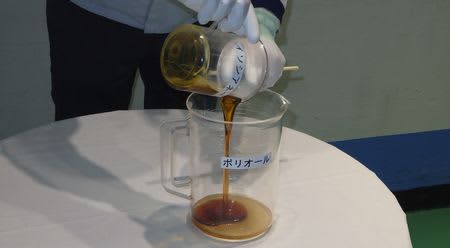
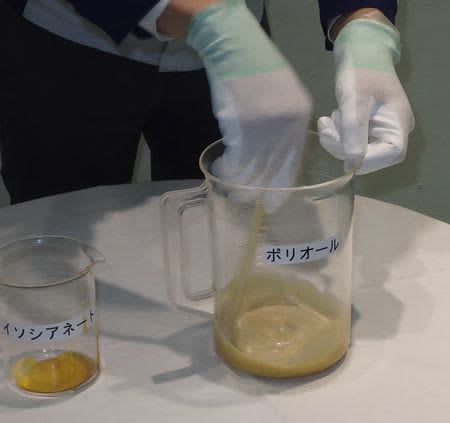
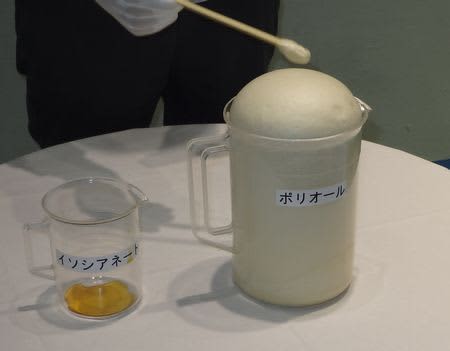
このポリオールとイソシアネートを冷蔵庫の壁面に注入して、化学反応させながら均一にウレタンを充填する。高度な技術を要する工程だ。
特に、庫内の大容量を確保するために、壁の厚さを薄くしてウレタンを充填する必要がある。だが、壁が薄くなるほど、ウレタン生成時にかかる圧力は約10トンにも及び、それを抑えるための機械や治具の開発も必要になる。
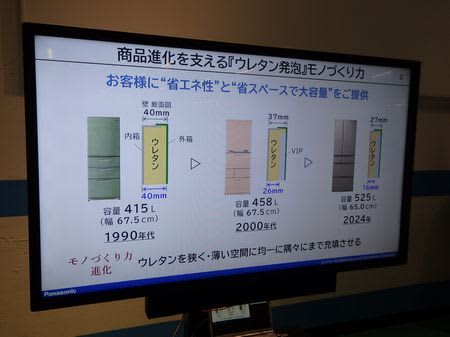
ウレタンの注入時間や広がっていく速度、注入する位置など精緻なシミュレーションも欠かせない。ウレタン注入ひとつをとっても、モノづくりのさまざな知見やノウハウが蓄積されているのだ。
多品種少量生産を支える「ミックス生産方式」
組み立てラインでは前述した各ユニットを、従業員が取り付ける。ここで威力を発揮するのが「ミックス生産方式」である。
実際に製造ラインを見ると、高さや容量、色、サイズの異なる冷蔵庫が次々とコンベアで運ばれる。当然、取り付ける部品のサイズや種類も機種により異なる。これを間違えることなく、しかも一定のスピードで取り付けていかなければならない。
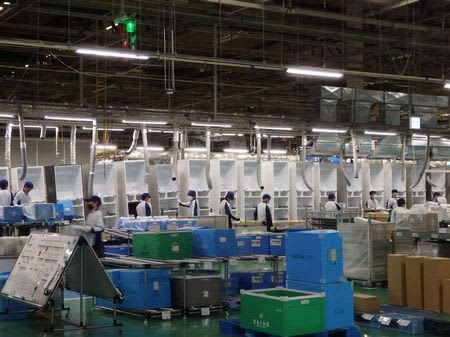
ラインにはかなり多くの従業員が作業に携わっているのがわかる。一人でもミスしたら、ラインは停止してしまい生産効率が下がる。草津工場では、そうならないようにバーコードとランプの光だけで、だれでも簡単に間違わずに取り付けられる仕組みを導入している。
多種多様な機種が混合してラインに流れてきても、一人として間違えることなく正確に生産する。それが、ミックス生産方式の神髄というわけだ。
高度な有資格者がコンプレッサを取り付ける
もう一つ重要な工程が、コンプレッサの取り付け作業。冷媒(ガス)漏れがないように、作業員がロウ付けという作業を行う。社内の高度な技術資格を取得した作業員だけが携われる。
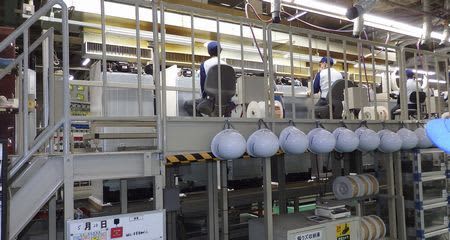
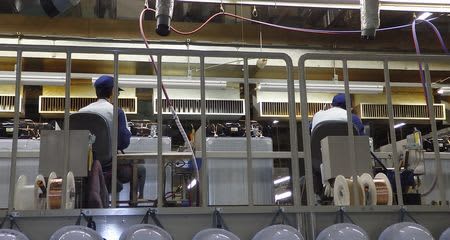
パナソニックの冷蔵庫は庫内スペースを有効活用するため、上部にコンプレッサを配置する「トップユニット方式」を採用している。そのためコンプレッサのロウ付けも、冷蔵庫の上部で作業員が作業しているのがわかる。
コンプレッサのロウ付けが終わったら、ガス漏れがないかをチェックする「ガスリーク検査工程」に移る。検査機を使ってすべてのロウ付け部分を全数検査。ガス漏れが発生した場合は、検査機の音と光、振動で警告を通知するという盤石の体制を整えている。
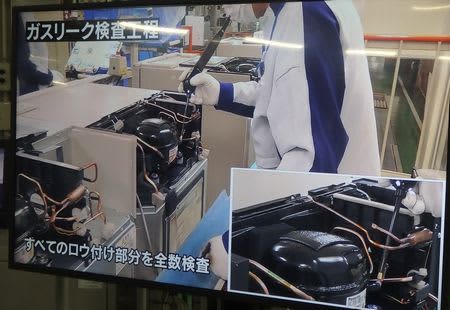
耐久性が求められる冷蔵庫
製品寿命8~12年という長い間使う冷蔵庫には、耐久性が求められる。特に毎日何度となく開閉するドアは、傾けば冷気漏れにつながるし、外れたら大けがにつながる。
そんなことが起きないよう、ドアを取り付けた後のビス締め工程では、ビス本数や締め付け強度の不足を機械で監視する。万が一NG判定が出たら、ラインは自動で停止する。
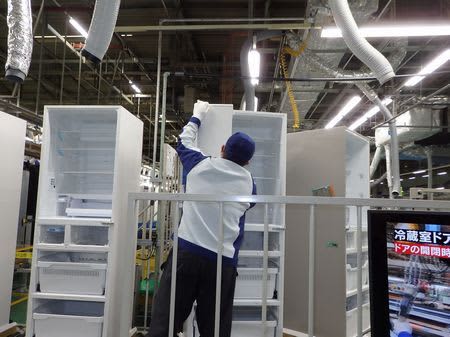
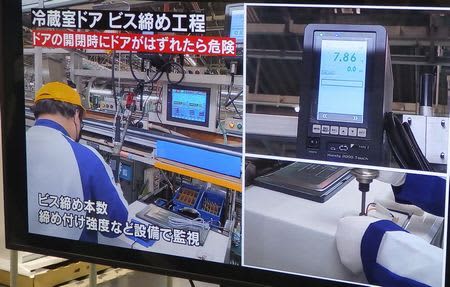
完成した後は従業員による目視チェックも行う。傷がないか、ドアの開閉に問題はないかなど、人間の感性による確認も行っている。
メディア初公開の検査試験室
今回の工場見学ツアーでメディアに初公開した三つの検査試験もあった。
「ガラスドア強度試験」では、ガラスドアにビール瓶をぶつけても傷がつかないことを検査する。ガラスドアはプライパンでたたいたぐらいでは割れないし、傷もつかない。万が一割れた場合も、ガラスが飛び散ることはなく、ひびだけが入る安全仕様になっている。
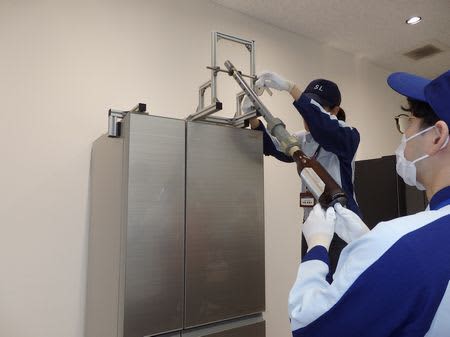
「冷却性能試験」では、過酷な環境でも食材が問題なく冷えるかを試験する。実際、温度35℃、湿度83%という、カメラレンズも一瞬で雲ってしまうような環境で、アイスクリームや飲料が冷えていた。
逆に5.2℃という寒い環境でも故障などの不具合は発生しない。この試験は、四季のある日本ならではとのことだ。
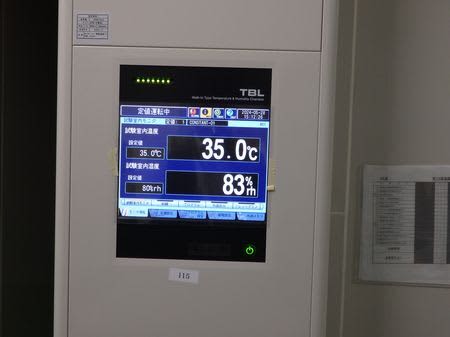
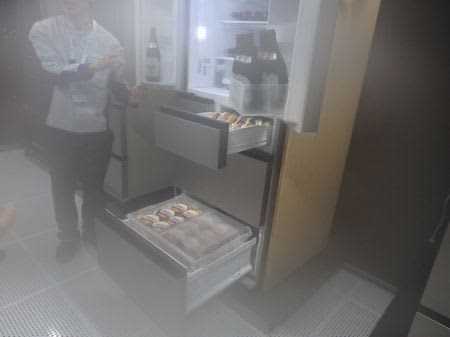
「ドア開閉試験」は、ドアに飲み物をびっしりと詰めた状態で、ドアの開閉を機械で繰り返す。パナソニック独自の野菜室が奥まで全開になる「ワンダフルオープン」も、機械で繰り返し開閉試験を行い、スムーズに開閉されるかを試す。
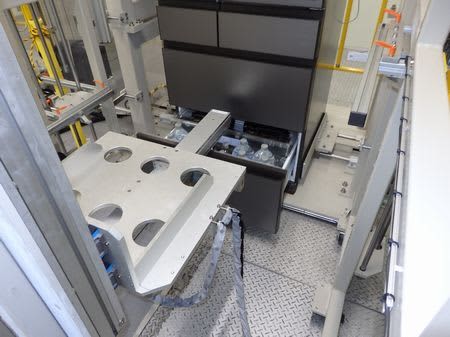
ミックス生産方式は最新の取り組みだが、一方で創業者である松下幸之助のときからあるという「お客様大事」を受け継いだ顧客視点の20カ条に及ぶ製品審査など、草津工場の取り組みの中には、変わるものと変わらずに受け継がれているものがある。
「圧倒的品位・品質の実現」をモノづくりの理想に掲げる草津工場は、「2年以内に世界トップクラスの生産効率を出せる」(太田常務)工場になるという。(BCN・細田 立圭志)