By 安蔵 靖志
5月28日にパナソニックの草津工場(滋賀県)にて同社冷蔵庫の生産現場の見学とセミナーが開催されました。ここでは最新モデル「CVシリーズ」の特徴と、同社の品質確保に向けた取り組みについてレポートしていきます。
国内トップシェアを誇るパナソニックの冷蔵庫の強みとは?
パナソニック くらしアプライアンス社が2023年3月に発売した「クラウド制御で実現 GX対応冷蔵庫 9Xシリーズ」は一般財団法人 省エネルギーセンターが主催する「2023年度省エネ大賞」の製品・ビジネスモデル部門で最高賞の「経済産業大臣賞」を受賞。
同社の常務の太田晃雄氏は、現在国内トップシェアの冷蔵庫事業をさらに伸ばしていくことで、「社会・地球全体の食文化を支えていきたい」と語りました。
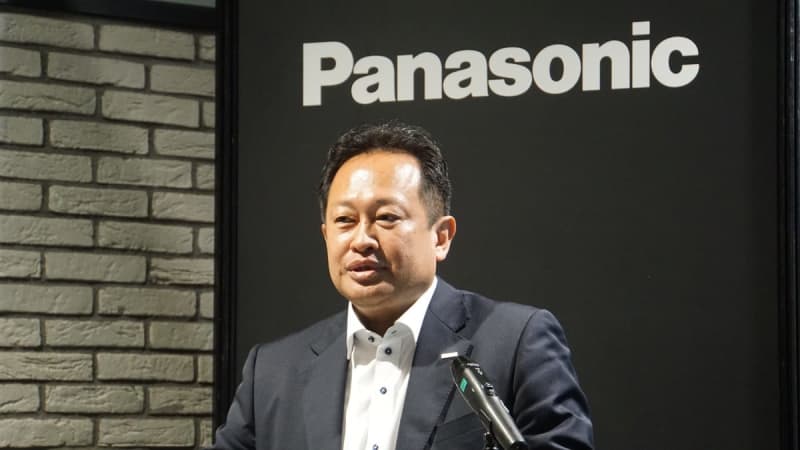
また、太田常務はパナソニックの冷蔵庫の強みとして「ものづくりのこだわり」と「社会・環境への貢献」の2つを掲げました。
一方、商品面では、スペースを有効活用できる「トップユニット方式」と引き出し収納を全開できる「ワンダフルオープン」などを挙げました。
「『トップユニット方式』は冷蔵庫の心臓部であるコンプレッサーを上に持ってくることで、お客様が手の届く範囲で最大限に収納しやすくしています。『ワンダフルオープン』は高級家具などで使用される高耐荷重のベアリング式レールによって、重い物がたくさん詰まっていてもたゆまず滑らかに引き出せるだけでなく、奥まで見えるのが我々の商品の特徴です。空間美と実用美ではデザインのこだわり、スキマレスでビスもないものづくりをご確認いただければと思います」(太田常務)
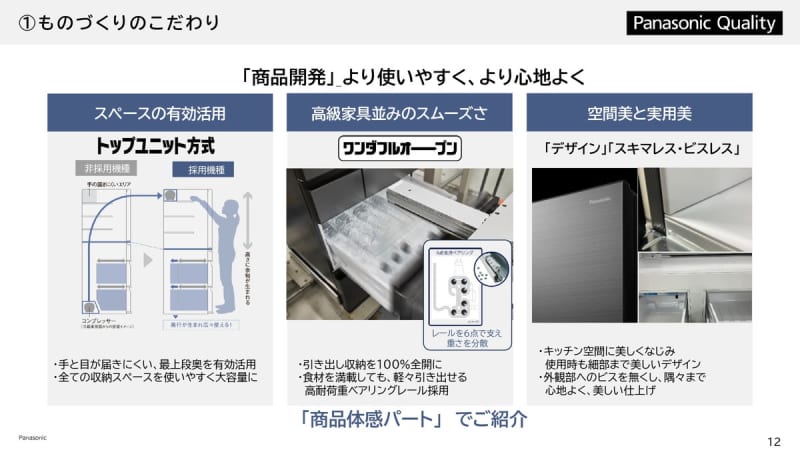
設計品質と製造品質、製品審査によって高品質を実現
工場での製造においては、設計品質と製造品質、製品審査によって高品質・高品位を実現していると太田常務は語りました。
「日本を含め非常にさまざまな環境、気温、湿度があるため、そこへ向けた冷却試験をしっかり実施しています。製造品質としては、この工場の特徴であるお客様の多種多様なニーズにタイムリーに対応する『ミックス生産』。それから生産の全台に対して性能検査や品質検査をすることで、品質を確保しています。製品審査は創業者である松下幸之助のお客様第一の精神を受け継ぐ部門で、設計部門や製造部門に対して、お客様視点で担当していく部門になっています」(太田常務)
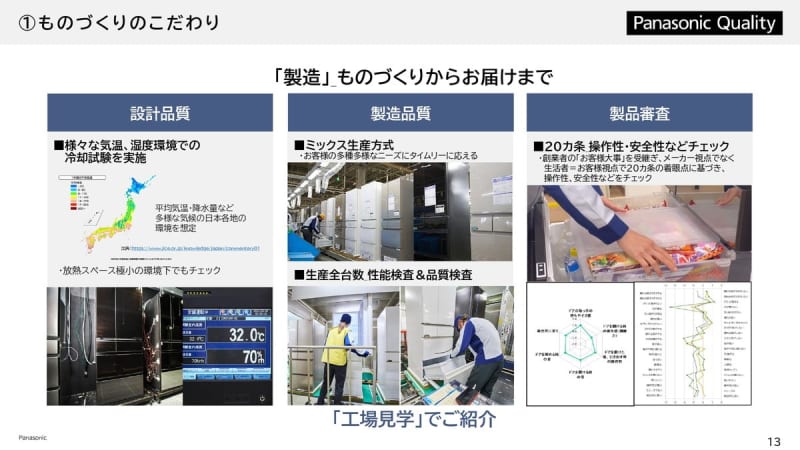
ミックス生産方式で効率的な多品種生産を実現
では、実際にどのようなものづくりをしているのか、工場内の様子を見ていきましょう。
冷蔵庫は「ドアブロック」「庫内ブロック」「冷却風路」「キャビネットブロック」「機械室」の大きく5つに分かれており、まずはキャビネットと内箱の間にウレタン発泡によって断熱材を充てんする工程が行われます。
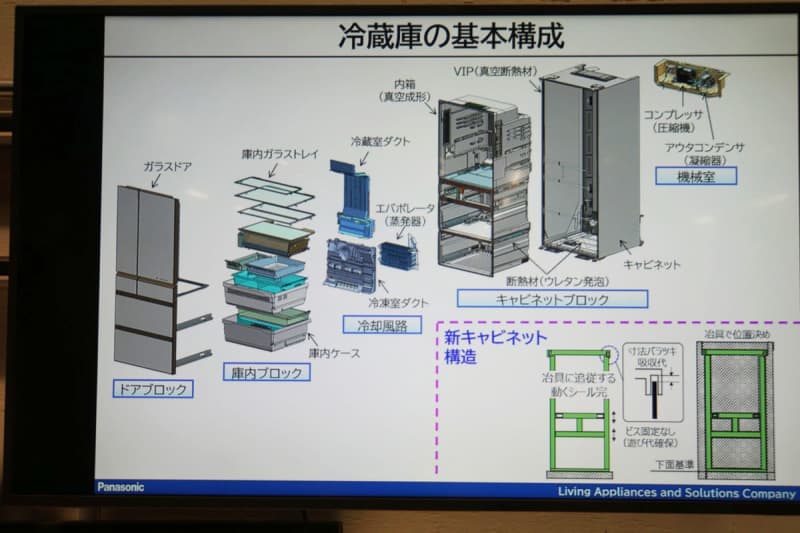
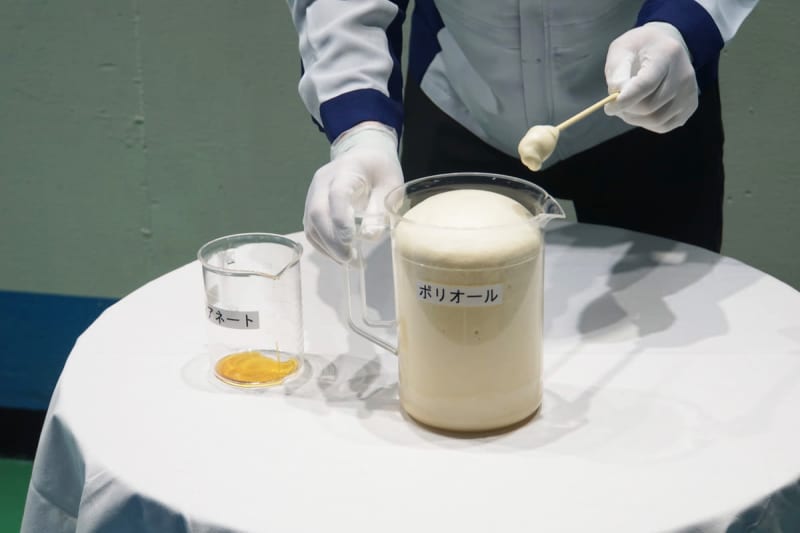
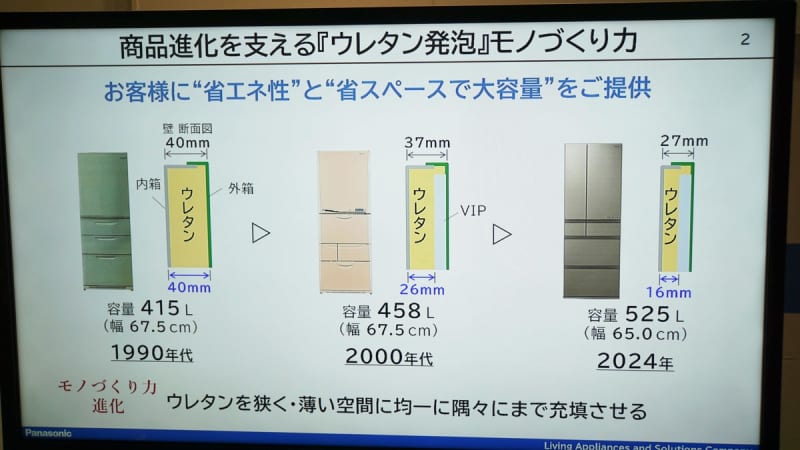
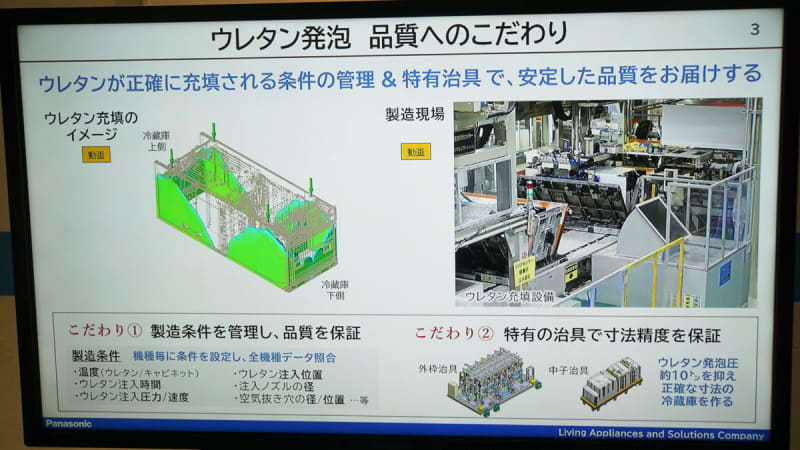
生産ラインでは、さまざまな型番の製品を一つのラインで製造する「ミックス生産」方式を採用しています。多品種を同時に製造できることで、多様化する顧客のニーズに素早く応えられるほか、在庫リスクの軽減が期待できます。
「高さの高いものや低いもの、横幅の広いものや狭いもの、奥行きが大きいものや小さいものと、いろいろなものがいっぺんに流れています。1ラインの中で同時に多品種を流しているのが一つの特徴です」(担当者)
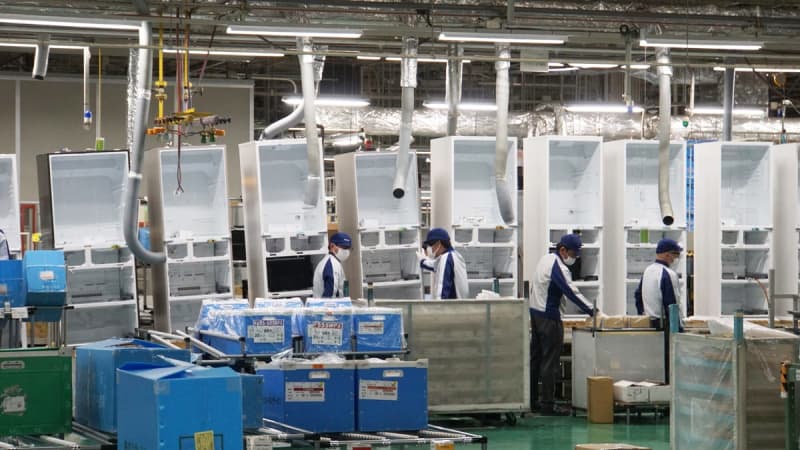
トップユニット方式のため、コンプレッサーの取り付け作業は階段を上がった場所で行われます。こちらではコンプレッサーと配管をロウ付けと呼ばれる作業で接合します。「非常に高い技能が必要になるため、社内で認定された人のみがロウ付け作業を行っています」(担当者)とのこと。
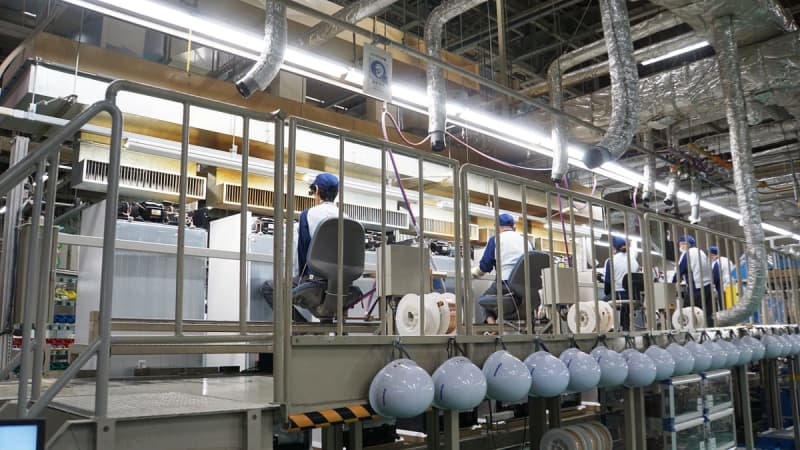
続いてドアの取り付けとビス締め作業を行います。どの製品にどのドアを取り付けるのかが指示されるので、それに従って取り付けていきます。
「取り付けに不備があると、ドアが落下してお客様に大きな怪我を与えてしまうことがありますので、安全工程としてビスの締め付け強度、ビスの本数に間違いがないかを専用のドライバーを使って管理しています」(担当者)
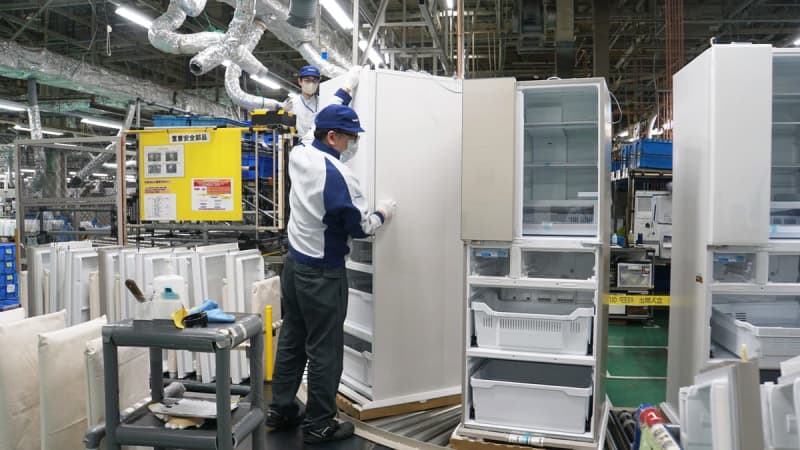
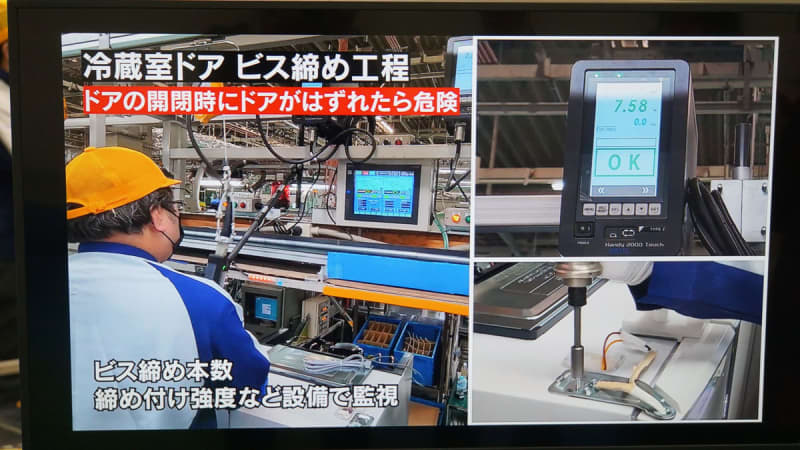
20年相当のドア開閉試験やガラスドアの強度試験などを実施
続いて、検査工程も見せてもらいました。ドア開閉試験では、家庭内での20年分に相当するドアの開閉を行う試験が行われます。
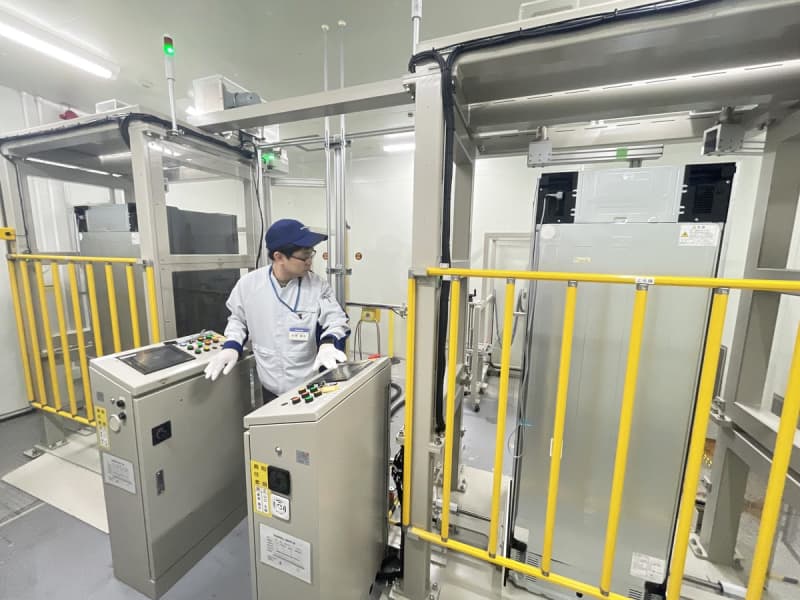
パッキンが冷えて硬くなり劣化しやすい冬場の寒い日の環境を想定し、約5℃の室内で1日24時間、約2か月かけてドアを開閉するとのことです。
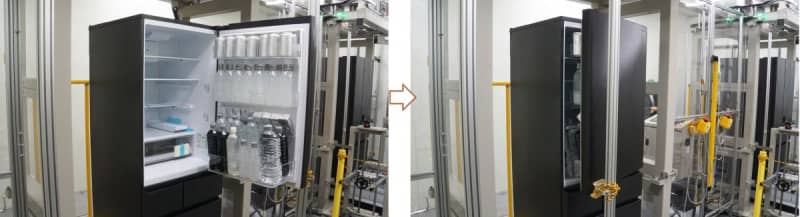
設計時に品質保証部門でもドア開閉試験を行うのですが、こちらでは最終量産直前に「基本的に全モデルを試験します」(担当者)とのこと。
「(引き出しの)レールは金属部品ですので、ちょっとでも金属がこすれるような音が鳴った場合に設計を見直すことがあります。1か所1ミリ削るなど、そのレベルで改善しています」(担当者)
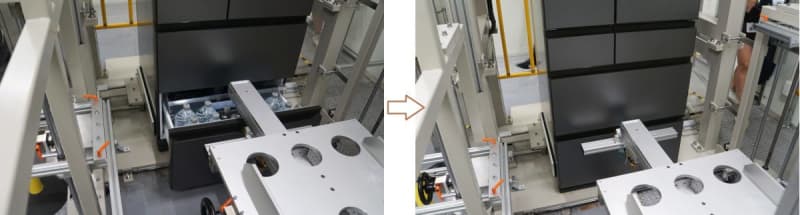
ガラスドアの強度試験も見学しました。ビール瓶が振り子の下に取り付けられており、ある程度の角度から振り下ろされたビール瓶がガラスドアに当たっても欠けや割れがないかを確認するというものです。
「人間が小走りした時の速さのイメージで、毎秒220cmほどの速さで衝突させて割れないかを確認しています。ガラスは強化処理で割れを防ぐとともに、万一割れた場合でもクモの巣状に細かく割れるように工夫されています。大きくて尖った破片によってお客様がケガをすることがないように設計されています」(担当者)
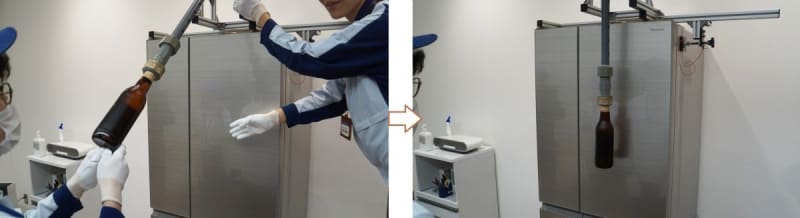
それにしても、ガラスドアの強度試験でビール瓶というのは少し意外ですが……。
「最初にガラスドアを開発した当時、ビール瓶以外にもいろいろなものをぶつけてみました。硬そうな鉄鍋でも、鉄は曲がって衝撃を吸収してしまいます。それに対してビール瓶は硬い上に変形しないので、衝撃をダイレクトにドア側に伝えることから、ビール瓶で試験をしています」(担当者)
一定の温度・湿度環境を保つ恒温室での動作試験も見学しました。全27部屋の恒温室で約300台の冷蔵庫を評価しており、その一つは室温約35℃、湿度約80%の高温多湿環境を再現する部屋でした。
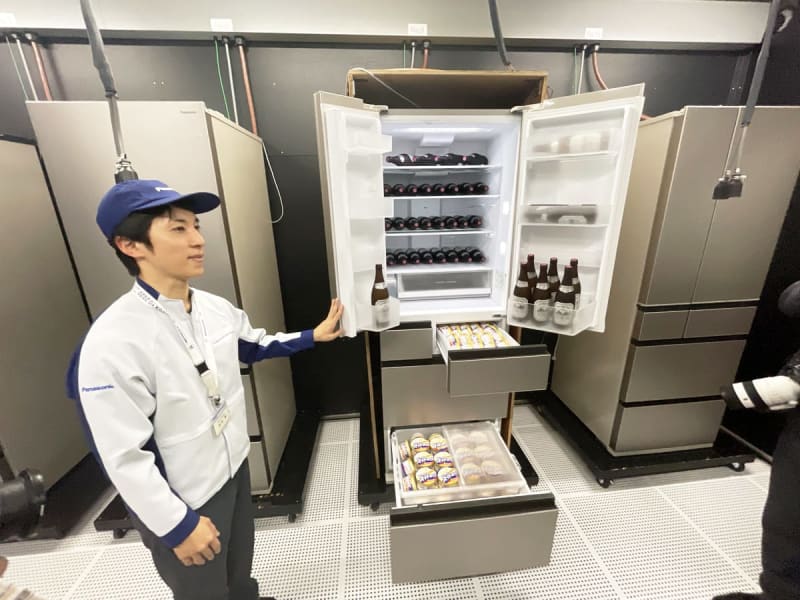
冷蔵庫の庫内には多数の温度センサーを配置しており、ドアを開閉した後の温度の変化を庫内の箇所ごとに確認しているとのこと。
「1日数十回ドアを開け閉めした後に少しずつ温度が上がっていくのですが、それが一定温度を超えずに冷やし始めてくれるかどうかを確認しています」(担当者)
どの部分が冷えにくいか、ということも分かるので、「冷気の流れの大きさを調整するなどの対策をしています」(担当者)とのことです。
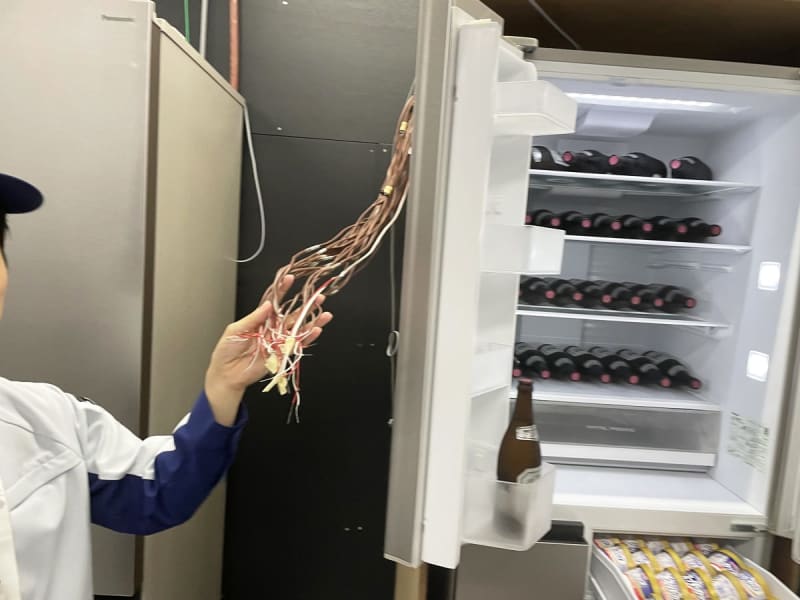
フードロスを削減するために「AIカメラ」を搭載
工場の製造工程におけるものづくりのこだわりについて紹介してきましたが、続いてはパナソニックの冷蔵庫の強みとして挙げられていた「社会・環境への貢献」について紹介しましょう。
省エネの面では、2024年発売の新モデル「CVシリーズ」と「HVシリーズ」で環境負荷低減にも寄与する新ウレタン発泡剤を採用。
「温暖化係数が従来商品の約10分の1で、部材でもCO2排出量の削減を取り組んでいます」(太田常務)
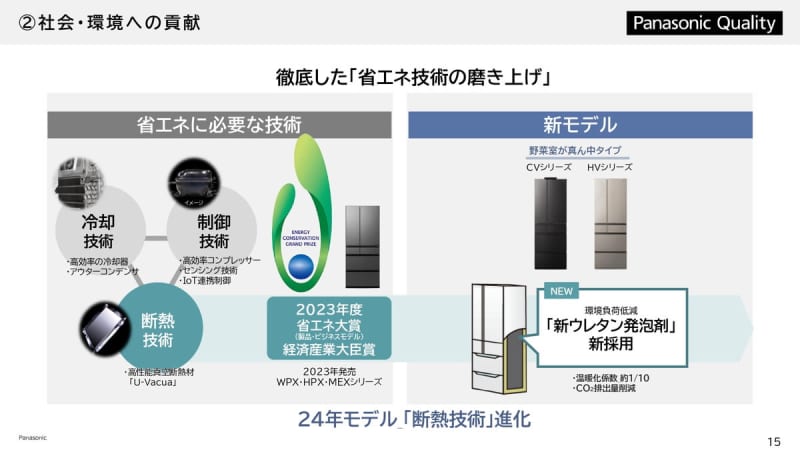
フードロスの削減に向けては、2024年発売の「CVシリーズ」で「冷蔵庫AIカメラ」を搭載しました。野菜室を撮影したカメラ画像からAIが野菜を自動認識してリスト化し、アプリに登録して早く使うべき野菜やレシピを提案してくれるというものです。
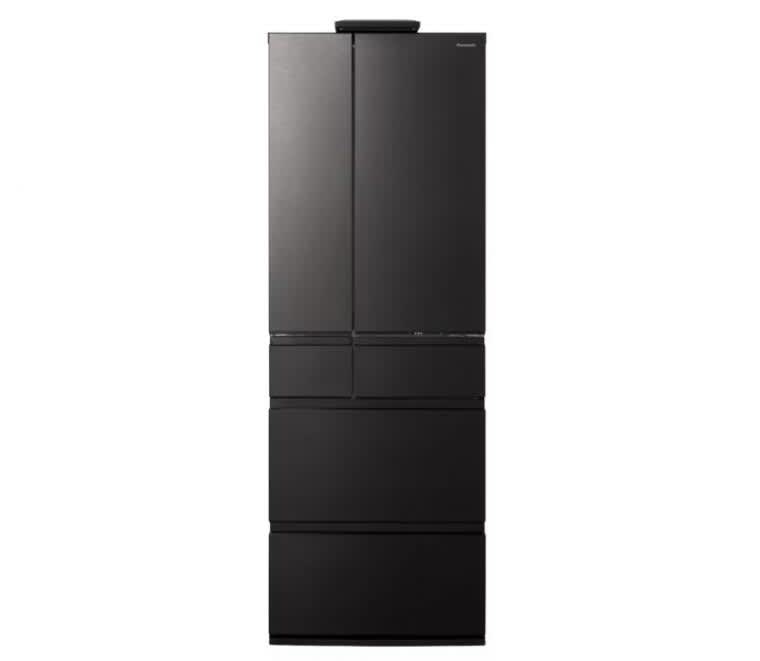
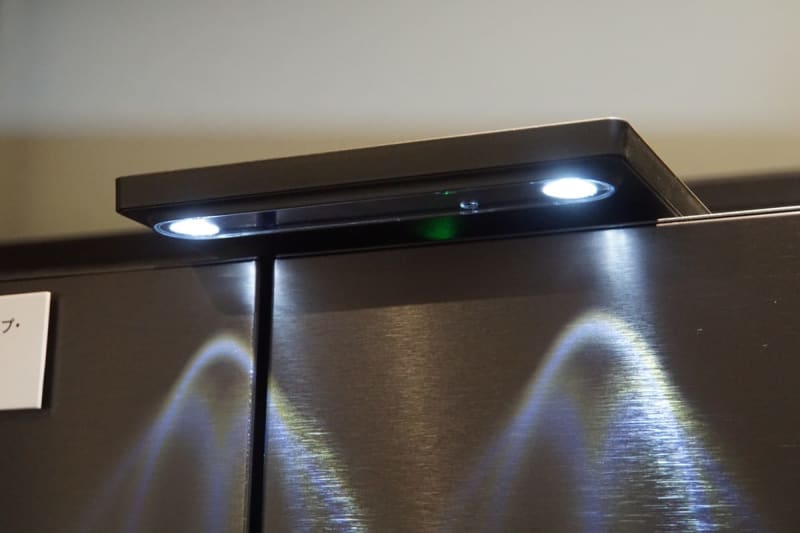
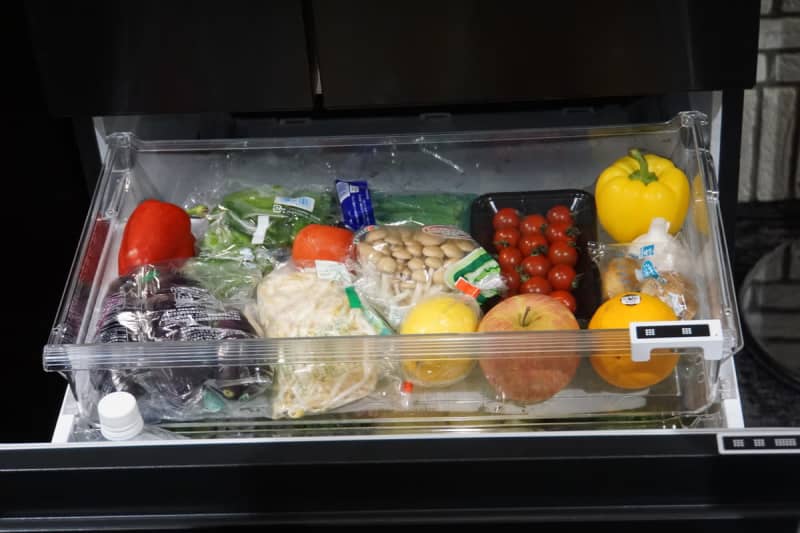
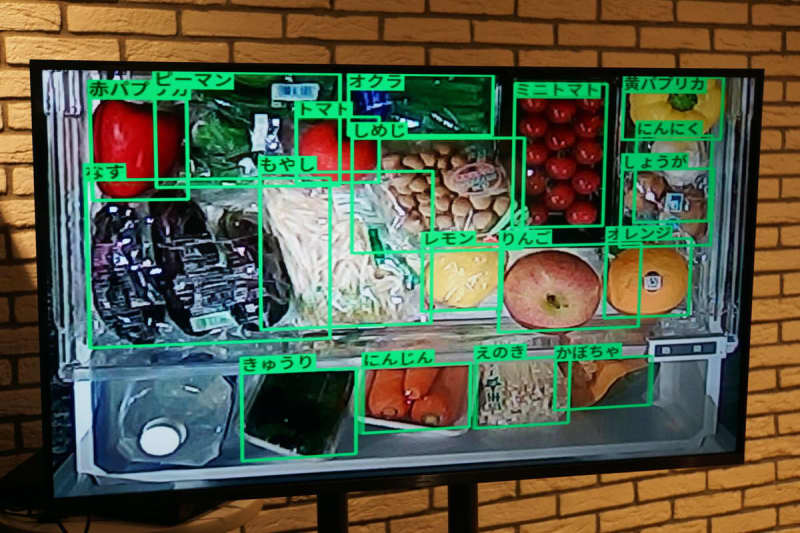
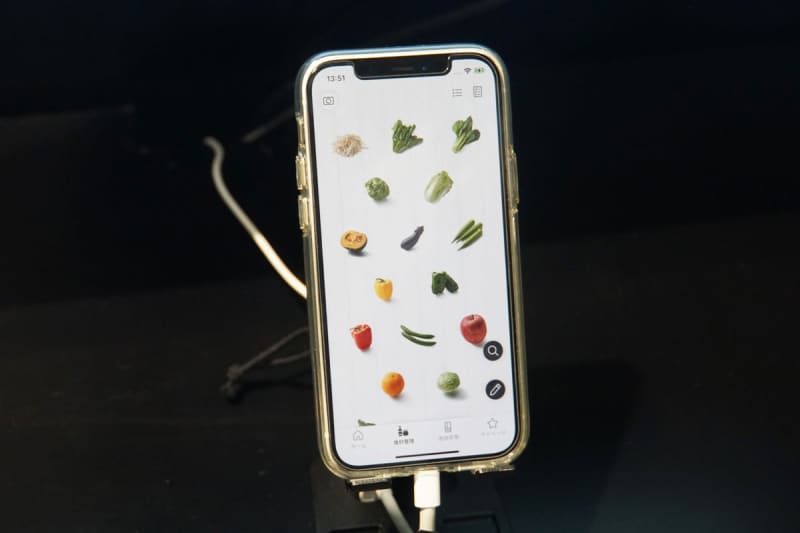
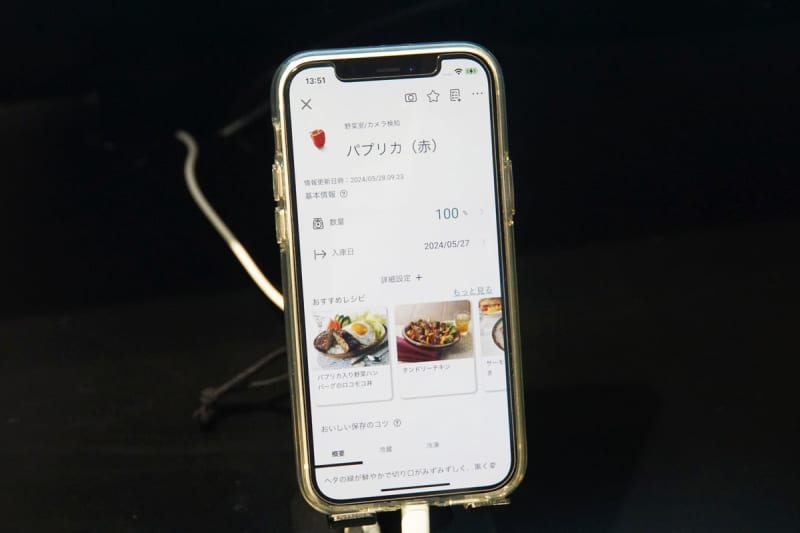
カメラで認識した野菜の登録や野菜の残りの量などは手動で変更する必要があるとのことですが、肉や魚よりもロスしやすい野菜をうまく活用できるという意味では頼りになりそうです。
海外メーカーでもカメラとAIで冷蔵庫内の食品を認識するという取り組みが進んでいますが、AIで徹底的に差別化を図るつもりはないと太田常務は語りました。
「AIはあくまでもお客様の使い勝手を良くする、フードロスを削減するという視点です。他社も含めて2つのカメラで引き出しまで見られるのは我々だけで、レシピ提案まで持っていったのは世界でも初だと思います。他社がCESでイノベーション賞を授賞したものより優れたものだと思っていますので、将来的には海外にも展開していきたいと考えています」(太田常務)
今回の工場見学とセミナーを通じて、同社がいかにユーザーの使い勝手の向上に努め、安全かつ環境に優しい製品の設計・製造を追求しているかがよくわかりました。今後の取り組みにも、ぜひ注目していきたいですね。
・
・
・