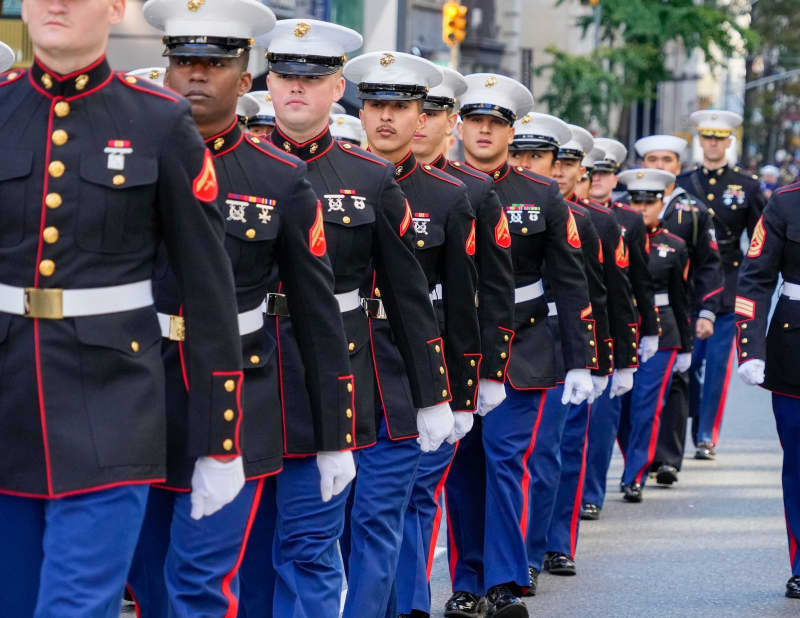
Ensuring the US Marine Corps is adequately outfitted with the right equipment, in top shape, even as its fighting needs evolve is no small feat. Today, that operation, undertaken by the US Marine Depot Maintenance Command (MDMC), is better oiled thanks to a transformation grounded in IT.
MDMC is responsible for maintaining, repairing, and calibrating Marine Corps equipment, including radios, weapons, and vehicles, both in the field and at huge depots in Georgia and California. The nearly 1-million-square-foot facilities, large enough to fit nearly 1,000 school buses in each, also provide engineering support, reverse-engineering capabilities, and parts and tool manufacturing services.
The MDMC’s primary goal has long been to get the most out of the equipment, with some expected to function for decades.
“We’re resetting that equipment to new or like-new condition so that we can get 20 or 30 years of use out of it,” says Vince Hutcherson, MDMC’s deputy commander.
But a couple of years ago, the MDMC realized it needed a wholesale IT upgrade to meet the challenges of repairing and modifying the huge range of equipment used by marines.
Limited automation and other IT capabilities at both depots, some of it decades old, had left MDMC to deal with repair delays, inaccurate information about equipment, and increased costs, Hutcherson says. The facilities were also seeing a trend toward more defects in products after maintenance and repair, instead of fewer, suggesting an upgrade was needed in inspection standards and quality control procedures as well.
Out with the old
In November 2022, MDMC launched a huge digital transformation project to bring modern IT capabilities, including RFID, AR/VR, and 5G networks to the two depots. The ongoing transformation has earned MDMC a 2024 CIO 100 Award for IT leadership and innovation.
“We’re really going from Industry 3.0, with having some automation in the workplace, to a workplace that’s able to leverage data to make decisions,” Hutcherson says. “This is an all-encompassing transformation.”
With such a huge scope, MDMC leaders decided to break the project up into three phases, according to MDMC’s application for the CIO 100 Award.
The first phase, lasting about 10 weeks, involved a rapid diagnostic of MDMC’s capabilities and needs. MDMC used professional services firm KPMG to analyze the depots’ KPIs and create a baseline of MDMC’s operating conditions, focusing on quality, materials, and costs. KPMG evaluated costs by product line, for example, and looked at variations in performance by facility and product line.
During the 16-week second phase, MDMC and KPMG worked together to design the digital transformation project. KPMG reviewed MDMC’s quality management and inventory management systems, its equipment condition, and its preventive maintenance processes. The two organizations came up with a list of gaps and risks and created a plan to fix problems and improve performance.
During the ongoing third phase, MDMC is implementing the recommendations and working to transform its maintenance infrastructure and procedures. MDMC has worked closely with KPMG to monitor progress.
RPA, RFID, robots, and more
The continuing digital transformation involves several technologies and vendors. MDMC is using robotic process automation and Microsoft Power Apps to streamline daily operations and reduce manual labor, according to MDMC’s application for the CIO 100 Award.
In addition, the depots are each deploying private 5G wireless networks to enable the network speeds necessary to monitor and manage the depot kitting, or parts bundling, operations. MDMC is also using Microsoft Dynamics 365 to run a complex warehouse and depot management system.
Under the new system, after the depot receives parts and gear, they are then barcoded and placed on an automated conveyer. The conveyer scans the barcodes and then deposits the parts in one of 32 kit locations.
srcset="https://b2b-contenthub.com/wp-content/uploads/2024/06/Marine-Depot-Maintenance-Command-Kitting-Warehouse.jpg?quality=50&strip=all 1800w, https://b2b-contenthub.com/wp-content/uploads/2024/06/Marine-Depot-Maintenance-Command-Kitting-Warehouse.jpg?resize=300%2C200&quality=50&strip=all 300w, https://b2b-contenthub.com/wp-content/uploads/2024/06/Marine-Depot-Maintenance-Command-Kitting-Warehouse.jpg?resize=768%2C512&quality=50&strip=all 768w, https://b2b-contenthub.com/wp-content/uploads/2024/06/Marine-Depot-Maintenance-Command-Kitting-Warehouse.jpg?resize=1024%2C683&quality=50&strip=all 1024w, https://b2b-contenthub.com/wp-content/uploads/2024/06/Marine-Depot-Maintenance-Command-Kitting-Warehouse.jpg?resize=1536%2C1024&quality=50&strip=all 1536w, https://b2b-contenthub.com/wp-content/uploads/2024/06/Marine-Depot-Maintenance-Command-Kitting-Warehouse.jpg?resize=1240%2C826&quality=50&strip=all 1240w, https://b2b-contenthub.com/wp-content/uploads/2024/06/Marine-Depot-Maintenance-Command-Kitting-Warehouse.jpg?resize=150%2C100&quality=50&strip=all 150w, https://b2b-contenthub.com/wp-content/uploads/2024/06/Marine-Depot-Maintenance-Command-Kitting-Warehouse.jpg?resize=1046%2C697&quality=50&strip=all 1046w, https://b2b-contenthub.com/wp-content/uploads/2024/06/Marine-Depot-Maintenance-Command-Kitting-Warehouse.jpg?resize=252%2C168&quality=50&strip=all 252w, https://b2b-contenthub.com/wp-content/uploads/2024/06/Marine-Depot-Maintenance-Command-Kitting-Warehouse.jpg?resize=126%2C84&quality=50&strip=all 126w, https://b2b-contenthub.com/wp-content/uploads/2024/06/Marine-Depot-Maintenance-Command-Kitting-Warehouse.jpg?resize=720%2C480&quality=50&strip=all 720w, https://b2b-contenthub.com/wp-content/uploads/2024/06/Marine-Depot-Maintenance-Command-Kitting-Warehouse.jpg?resize=540%2C360&quality=50&strip=all 540w, https://b2b-contenthub.com/wp-content/uploads/2024/06/Marine-Depot-Maintenance-Command-Kitting-Warehouse.jpg?resize=375%2C250&quality=50&strip=all 375w" width="1240" height="827" sizes="(max-width: 1240px) 100vw, 1240px">
Jennifer Napier, USMC
Once a kit is complete, an RFID tag is assigned to track it across the facility, and mobile robots transport the kits to assigned drop zones.
“We have a desire to run the business more efficiently and more effectively, and to do that, we need to have better visibility over where the costs are and where we are in performance, based on plan,” Hutcherson says. “To have that type of data in real time gives us a better picture of the changes we need to make.”
Saving time, saving money
MDMC also went through a business process management exercise, using interviews and workshops, to identify ways to improve processes. The exercise created some huge time savings:
- A standardized and digitized receipt process that reduced receipt processing time from about six minutes for each item received from the Defense Logistics Agency to about 10 seconds.
- An automated Disassembly Disposition Report (DDR) process using robotic process automation that reduced the processing time to issue work orders for procurement from one week per commodity to six hours.
The digital transformation has resulted in several other major improvements to depot operations, in addition to warehouse automation and better tracking of parts and materials.
Even though the project isn’t finished, the average time to fix vehicles on site has dropped from 281 days to less than 150 days, driven by better visual managements tools and quality control. In addition, post-repair inspections have observed a 60% reduction in defects.
Finally, there’s the bottom line. The deployment of robotic process automation and Microsoft Power Apps has reduced annual costs by an estimated $10.4 million, and the improved parts receipts process has saved about $4 million.
Cost reduction was a big driver of the digital transformation, Hutcherson says. “We want to ensure the operation is financially viable so we’re there when the Marine Corps and the country needs us,” he says.
Hutcherson sees two improvements having the biggest potential impacts. The view from inside MDMC is that the new warehouse management will create huge long-term benefits and lead to major cost savings and efficiency. Many marines in the field, however, have expressed interest in AR/VR for the remote maintenance and repair possibilities. Using AR or VR headsets, technicians at a US depot will be able to help marines in the field fix many equipment problems, he says.
Ultimately, the changes will help the MDMC keep up with the Marine Corps as it adapts to new ways of fighting wars. “We want to ensure that the command is relevant in the future,” Hutcherson says. “As the Marine Corps’ warfighting philosophy changes, we need to make sure that we’re changing, too.”