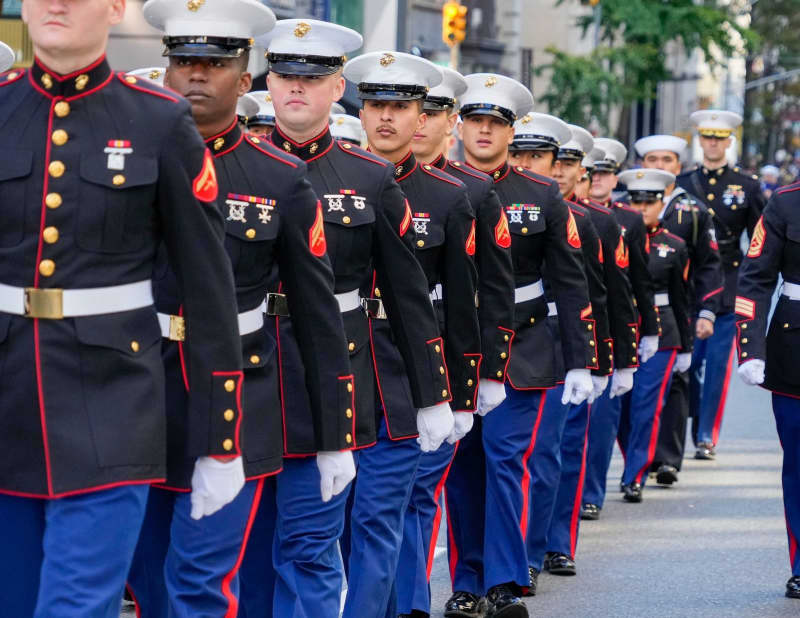
Garantizar que el Cuerpo de Marines de los Estados Unidos (EE.UU) cuente con el equipamiento adecuado, en plena forma, incluso a medida que evolucionan sus necesidades de combate, no es tarea fácil. Hoy en día, esa operación, llevada a cabo por el Mando de Mantenimiento de los Depósitos de los Marines de EE.UU. (MDMC), está mejor engrasada gracias a una transformación basada en las TI.
El MDMC es responsable del mantenimiento, reparación y calibración de los equipos del Cuerpo de Marines, incluidas radios, armas y vehículos, tanto sobre el terreno como en los enormes depósitos de Georgia y California. Las instalaciones de más de 300.000 metros cuadrados también proporcionan apoyo de ingeniería, capacidades de ingeniería inversa y servicios de fabricación de piezas y herramientas.
El principal objetivo del MDMC es, desde hace tiempo, sacar el máximo partido de los equipos, algunos de los cuales se espera que funcionen durante décadas.
“Estamos restaurando esos equipos para que sean nuevos o seminuevos, de modo que podamos utilizarlos durante 20 o 30 años”, afirma Vince Hutcherson, comandante adjunto del MDMC. Pero hace un par de años, el MDMC se dio cuenta de que necesitaba una modernización informática a gran escala para hacer frente a los retos de reparar y modificar la enorme variedad de equipos que utilizan los infantes de marina.
La limitada automatización y otras capacidades informáticas de ambos depósitos, algunas de ellas con décadas de antigüedad, habían hecho que el MDMC tuviera que lidiar con retrasos en las reparaciones, información inexacta sobre los equipos y un aumento de los costes, afirma Hutcherson. En las instalaciones también se observaba una tendencia a la aparición de más defectos en los productos tras el mantenimiento y la reparación, en lugar de menos, lo que sugería que también era necesaria una actualización de las normas de inspección y los procedimientos de control de calidad.
Fuera lo viejo
En noviembre de 2022, MDMC puso en marcha un enorme proyecto de transformación digitalpara dotar a los dos almacenes de modernas capacidades informáticas, como RFID, AR/VR y redes 5G. La transformación en curso le ha valido a MDMC el premio CIO 100 de 2024 por su liderazgo e innovación en TI en la versión estadounidense que celebra esta publicación.
“Realmente estamos pasando de la Industria 3.0, con tener cierta automatización en el lugar de trabajo, a un lugar de trabajo que es capaz de aprovechar los datos para tomar decisiones”, dice Hutcherson. “Se trata de una transformación integral”.
Con un alcance tan grande, los líderes de MDMC decidieron dividir el proyecto en tres fases, según la solicitud de MDMC para el Premio CIO 100.
La primera fase, de unas 10 semanas de duración, consistió en un rápido diagnóstico de las capacidades y necesidades del MDMC. MDMC recurrió a la empresa de servicios profesionales KPMG para analizar los indicadores clave de rendimiento de los almacenes y crear una base de referencia de las condiciones operativas de MDMC, centrándose en la calidad, los materiales y los costes. KPMG evaluó los costes por línea de producto, por ejemplo, y examinó las variaciones de rendimiento por instalación y línea de producto.
Durante la segunda fase, de 16 semanas de duración, MDMC y KPMG trabajaron juntos para diseñar el proyecto de transformación digital. KPMG revisó los sistemas de gestión de calidad y gestión de inventarios de MDMC, el estado de sus equipos y sus procesos de mantenimiento preventivo. Las dos organizaciones elaboraron una lista de carencias y riesgos y crearon un plan para solucionar los problemas y mejorar el rendimiento.
Durante la tercera fase en curso, MDMC está aplicando las recomendaciones y trabajando para transformar su infraestructura y procedimientos de mantenimiento. MDMC ha colaborado estrechamente con KPMG para supervisar los avances.
RPA, RFID, robots y mucho más
La continua transformación digital implica varias tecnologías y proveedores. MDMC está utilizando la automatización de procesos robóticos y Microsoft Power Apps para agilizar las operaciones diarias y reducir el trabajo. Además, los almacenes son cada vez más eficientes. Y es que cada uno de ellos está desplegando redes inalámbricas 5G privadas para permitir las velocidades de red necesarias para supervisar y gestionar las operaciones de kitting o agrupación de piezas. MDMC también utiliza Microsoft Dynamics 365 para gestionar un complejo sistema de gestión de almacenes y depósitos.
Con el nuevo sistema, una vez que el almacén recibe las piezas y los equipos, se les asigna un código de barras y se colocan en un transportador automatizado. El transportador escanea los códigos de barras y deposita las piezas en una de las 32 ubicaciones de los kit.
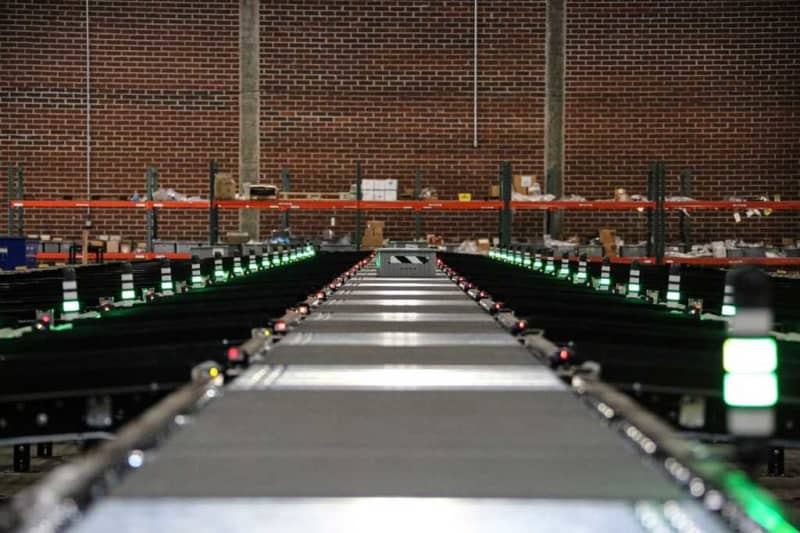
Jennifer Napier, USMC
Una vez que el paquete está completo, se le asigna una etiqueta RFID para seguirlo por las instalaciones, y robots móviles transportan los kit a las zonas de entrega asignadas.
“Queremos gestionar la empresa de forma más eficiente y eficaz y, para ello, necesitamos tener una mejor visibilidad de los costes y el rendimiento en función del plan”, afirma Hutcherson. “Disponer de ese tipo de datos en tiempo real nos da una mejor idea de los cambios que tenemos que hacer”.
Ahorrar tiempo, ahorrar dinero
MDMC también llevó a cabo un ejercicio de gestión de procesos empresariales, mediante entrevistas y talleres, para identificar formas de mejorar los procesos. El ejercicio supuso un enorme ahorro de tiempo:
- Un proceso de recepción estandarizado y digitalizado que redujo el tiempo de tramitación de la recepción de unos seis minutos por cada artículo recibido de la Agencia Logística de Defensa a unos 10 segundos.
- Un proceso automatizado de Informe de Disposición de Desmontaje (DDR). Utilizando la automatización de procesos robóticos, redujo el tiempo de procesamiento para emitir órdenes de trabajo para la adquisición, de una semana por mercancía a seis horas.
La transformación digital ha dado lugar a otras mejoras importantes en las operaciones de depósito, además de la automatización de almacenes y un mejor seguimiento de piezas y materiales.
Aunque el proyecto no ha terminado, el tiempo medio de reparación de vehículos in situ ha bajado de 281 días a menos de 150, gracias a la mejora de las herramientas de gestión visual y control de calidad. Además, en las inspecciones posteriores a la reparación se ha observado una reducción del 60% de los defectos.
Por último, está el balance final. La implantación de la automatización de procesos robóticos y Microsoft Power Apps ha reducido los costes anuales en unos 10,4 millones de dólares, y la mejora del proceso de recepción de piezas ha ahorrado unos 4 millones de dólares.
La reducción de costes fue uno de los principales impulsores de la transformación digital, afirma Hutcherson. “Queremos asegurarnos de que la operación sea financieramente viable para estar ahí cuando el Cuerpo de Marines y el país nos necesiten”, afirma.
Hutcherson considera que hay dos mejoras que pueden tener las mayores repercusiones. La opinión desde dentro del MDMC es que la nueva gestión de almacenes generará enormes beneficios a largo plazo y supondrá un importante ahorro de costes y eficiencia. Sin embargo, muchos marines sobre el terreno han expresado su interés en la RA/VR por las posibilidades de mantenimiento y reparación a distancia. Utilizando auriculares de RA o RV, los técnicos de un almacén estadounidense podrán ayudar a los infantes de marina sobre el terreno a solucionar muchos problemas de los equipos, afirma.
En última instancia, los cambios ayudarán al MDMC a mantenerse al día con el Cuerpo de Marines a medida que se adapta a las nuevas formas de luchar en las guerras. “Queremos asegurarnos de que el mando sea relevante en el futuro”, dice Hutcherson. “A medida que cambia la filosofía de lucha bélica del Cuerpo de Marines, tenemos que asegurarnos de que nosotros también estamos cambiando”.