JFEスチールは4日、自動車の車体組み立てに使われる新しいスポット溶接技術を相次ぎ開発したと発表した。超ハイテン(高張力鋼板)に対応する4種類の高機能なスポット溶接技術で、溶接品質の向上や車体の設計自由度向上が可能になる。車体軽量化に有効な超ハイテンをより使いやすくする溶接技術として超ハイテンとセットでユーザーに提案し、鉄を最大限活用した次世代自動車の開発を後押しする。
車体の設計自由度向上
スポット溶接は、重ね合わせた鋼板を二つの電極で挟み込んで大電流を流し、鋼板を溶かして点溶接する溶接手法。他の溶接手法より施工のコストや効率に優れるため、自動車製造で最も多く使われており、車1台に3千~6千点のスポット溶接部があるとされる。
ただ、これまでのスポット溶接を超ハイテンにそのまま適用するのは難しい。超ハイテンは板厚が薄いため車体軽量化に有効。一方で、薄くても強い特性を持たせるために複雑な金属組織を造り込んでおり、従来のスポット溶接では品質や施工管理が難しい。そのため超ハイテンを使う場合は車体の構造設計に制約が生じていた。
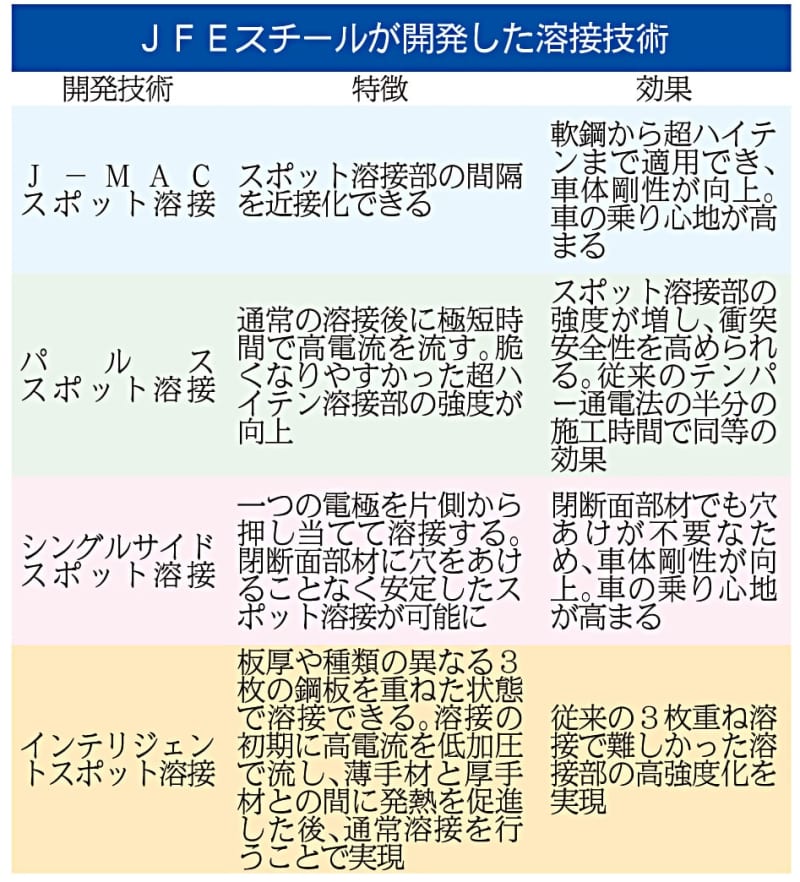
JFEが開発した新しい高機能スポット溶接技術は、(1)スポット溶接部間隔の近接化により剛性を高める「J―MACスポット溶接」(2)溶接部の強度を高める「パルススポット溶接」(3)効率施工で剛性を確保できる「シングルサイドスポット溶接」(4)3枚重ねの鋼板に対応する「インテリジェントスポット溶接」―の4種類の技術で、いずれも超ハイテンの溶接品質を高めるのに有効だ。
4種類のうち、J―MAC、シングルは基本技術を確立した段階。現在、ユーザーの工程で実用化に向けた検証を進めている。パルス、インテリジェントはすでに実用化した。
パルスとインテリジェントは基本的にユーザーの既存の溶接ロボットを活用できる。シングルとJ―MACは新しい溶接ロボットへの移行や改造が必要になる。