大手自動車部品メーカーのヨロズ(本社・横浜市)にとり国内最大の生産拠点となるヨロズ大分(本社・大分県中津市)が最新の大型プレス機と自動化技術の導入を進めている。熱延鋼板を加工した足回り部品のサスペンション造りを究め続けてきた同社。その技術がもたらすものは何か、現地で取材した。(黒澤 広之)
ヨロズ大分が操業を開始したのは1977年1月。日産自動車の九州進出に伴い、当時は萬自動車工業・中津工場としてスタートした。
工場の眼の前は中津港で、近隣には福岡県苅田町の日産自動車九州や日産車体九州、同じ中津市にあり車で15分ほどの場所にあるダイハツ九州、そして本州に渡るとマツダ本社工場や防府工場がある。
さらに、その先にはルノー・日産アライアンス入りした三菱自動車工業の水島製作所があり、次期モデル車からRRビームの納入を開始する予定だ。
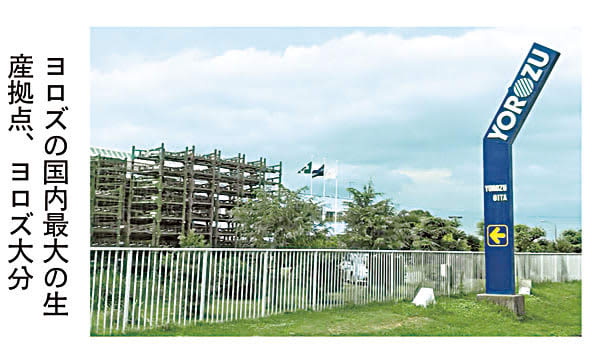
ヨロズ大分の売上高は前期実績で190億9800万円。販売先の約9割は日産グループ向けで、次いで6%がマツダ、4%弱がダイハツとなっている。日産の好調を反映し、ヨロズ大分の売上高も年々増加が続いている。
ヨロズ大分の製品もやはり日産向けが中心。特に主力と位置付けられるのがクロスオーバーSUVの「エクストレイル」向けサスペンションメンバーだ。このほか共通プラットフォームのミニバン「セレナ」向けや、日産車体が造るSUV「パトロール」ではヨロズ最大級の40キログラムという厚手のサスペンションが採用されている。
ヨロズ大分の従業員は今年3月末時点で456人。うち製造課は402人で、生産工程は大きく分けて(1)鋼板のプレス(2)溶接・組立(3)塗装―の3つがある。
場内に入ると、プレスエリアではそこかしこでプレス機の鋼板を打ち抜く音が絶え間なく響き、その繁忙ぶりを物語っている。現在の鋼材使用量は月間4千トン。鋼材の使い方では、打ち抜く部材の間を可能な限り狭くし、歩留まり向上・スクラップの最少化を目指している。
数々のプレス機を持つヨロズ大分だが、これまではブランキングプレスで500トン、トランスファープレスでは1200トンが最大。プレス機の規模が小さく、大きな部品は外部に発注して持ち込む必要があった。
この泣きどころ解消に向け、新設したのがコマツ製の3500トンハイブリッド・サーボ・モジュール・トランスファープレスと1200トンブランキングプレスだ。金型置き場だった場所に40メートル×84メートルの建屋を新たに増築し、これら新鋭の大型プレス機を導入。9月末から10月末にかけて立ち上げていく。
3500トンサーボプレスは、ヨロズが世界各地で進めてきた大型プレス機投入戦略の一環。ヨロズ大分は米国のアラバマ、メキシコ第2工場、中国の広州と武漢に続く5拠点目の導入だ。つまり国内では最大のプレス機となり、同機によって大きな部品を内製化し「エクストレイル」向けを一貫で造り込めるようになる。
3500トン機の特徴は、2000+1500トンのハイブリッドで同時に12工程を加工でき、加工の精度も高まっている点だ。多忙な他のプレス機の負荷を低減でき、サーボプレスで超ハイテン(高張力鋼板)の難成型にも対応できる。
志藤昭彦会長兼CEOは「当社が使う鋼板は厚く重いものが多い。軽量化にはハイテンを使う必要があるが、スプリングバックが大きく形状も従来の機械では出しにくかった。大型サーボプレス機で我々の望む形にでき、12工程をこなせるため別のプレス機へ持っていく必要がなくなる。無駄な在庫も減らせる」と利点を語る。
また志藤健社長兼COOは「通常、材料費は6割ほどを占めるが、ヨロズ大分は大きな部品を買っていたためこの購入費が高かった。内製化で固定費を減らすことで、設備投資の償却には20年もかからないだろう」と、早期の投資回収にも自信を見せている。
同機の採用は世界で5台目だが、ヨロズ大分では初の取り組みとして3500トン機の上部にカメラを設置し、2台のロボットで部材を投入する自動化を図っている。従来は1~2人を配置していた工程を無人化するもので「この手のトランスファープレス機にロボットでバラを投入するのは業界初ではないか」(佐藤和己副会長兼CCO)とされている。
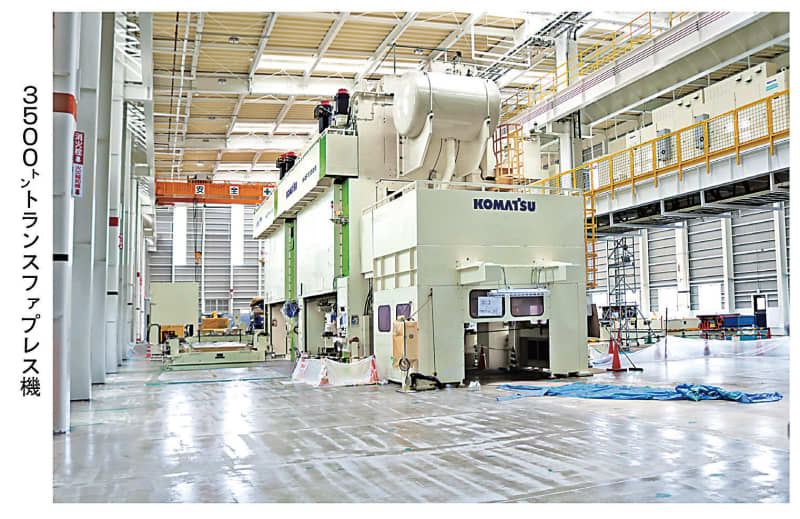
世界最先端のサスペンション造り追究
溶接組立、1ラインに1人
生産ラインの自動化・無人化は、溶接・組立工程でも行われている。2016年にエクストレイルおよびセレナ向けの2つの自動化ラインが稼働しており、アセンブリや部品のセット、溶接、検査は全てロボットなどが行っている。
シューターへの部材投入は人が行うが、これは兼任で複数ラインを巡回するため、ラインの専任者は1人だけだ。従来のラインでは7人ほど置いていた作業を大きく省人化し、ヨロズエンジニアリング(本社・山形県東田川郡)で開発した小型自動搬送機によって組立スペースも削減。生産効率は1・25倍へ向上させた。
志藤会長は「省人化だけでなく、自動化で決まった数量を確実にこなし、品質も一定である意義が大きい」と語る。ただし、その実現には同社が培ってきた高度な技術の裏付けがあることを強調する。「人間同士なら干渉しようとすれば避けるが、ロボットは干渉した瞬間に止まってしまう。この精度、信頼性をクリアする技術は本当に難しく、相当な投資をしてきた」と自負を見せる。
一方で無人化を進めながらも、技能教育エリアでは新入社員へアーク溶接の技能を徹底的に教え込んでいる。実際の溶接作業はロボが行うものの、品質の判断力を鍛えるべく手作業による実習も大切にしている。
自動化で生産拡大
ヨロズ大分の池内亮蔵社長によると、現状の工場はフル生産で、勤務時間は2直・残業3時間と「昼夜ほぼ操業がつながっている状態」と話す。今後は新プレス機の稼働や自動化の割合が増えてくるため、生産量はさらに増える見通しだ。
思うように人の採用ができない昨今、自動化・無人化の技術は大きなアドバンテージになる。
もちろん完全に人が要らなくなる訳ではない。「単純なラインの作業者は減っても、ラインの設計者や機械の維持・保全を担う人材は必要」(志藤会長)だ。ただ、人が担う仕事は着実に変わっていく。人の手では重くて運べない部材をロボでハンドリングする設計といった「人をロボへ置換するのでなく、始めからロボありきで構想」(志藤社長)することで、安全かつ効率的な作業が実現することになる。こうした自動化を通じ「プレスや溶接の仕事が洗練されて、いい人材が採れるようになるのでは」(佐藤副会長)とも期待されている。
日本国内だけでなく最近では中国でも採用難や人件費の上昇が顕在化しており、自動化技術はグローバル展開の上でも重要になってきている。「作業によって無人化に向いているところと、そうでないところがある」(志藤会長)中で、これを見極めながら世界最先端のサスペンション造りを追究していく考えだ。
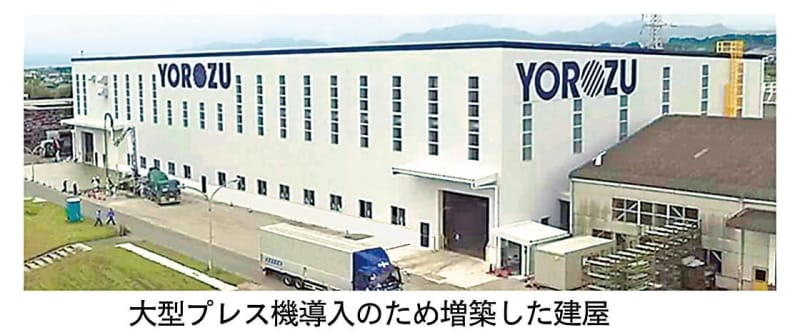
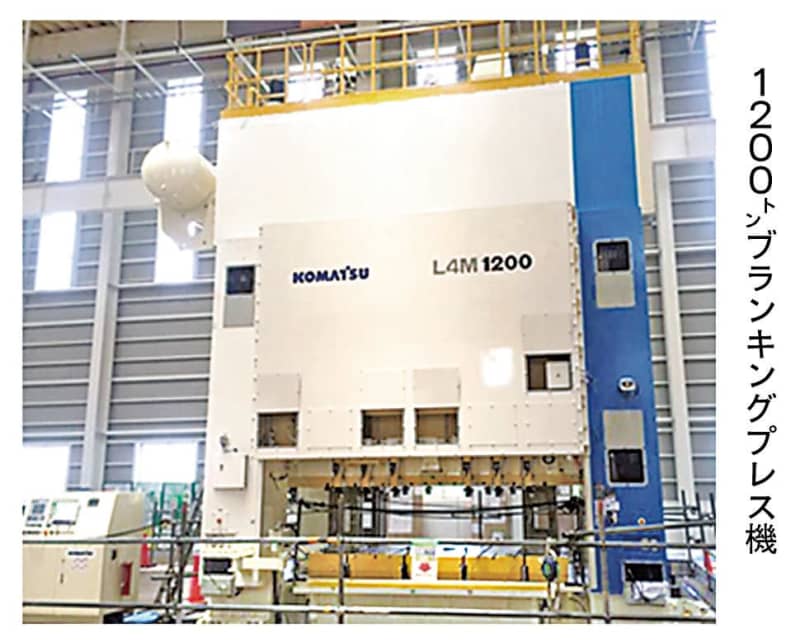